Welding is a skill that requires precision and attention to detail. Even experienced welders can encounter defects that compromise the quality and integrity of their work. In this troubleshooting guide, we’ll cover the most common welding problems and how you can easily fix them.
Porosity
Porosity is a common welding defect characterized by small holes or cavities in the weld metal. These pores are caused by trapped gas bubbles that later solidify in the weld.
- Causes. The primary cause of porosity is contamination, which can include oil, grease, rust, or moisture on the base metal or filler material. Improper gas shielding can also lead to porosity, either due to insufficient gas coverage or incorrect gas flow rate. Finally, incorrect welding techniques, such as holding the torch too far or using improper electrode angles can make the issue worse.
- Fixes. A welding troubleshooting tip for preventing porosity is to ensure all your materials are clean and dry before welding. You should also adjust the gas flow rate and check for leaks in the gas supply system.
Cracks
Cracks are another critical welding problem that can weaken your weld and ruin all your hard work. Cracking can occur during or after welding, in different forms such as hot and cold cracks.
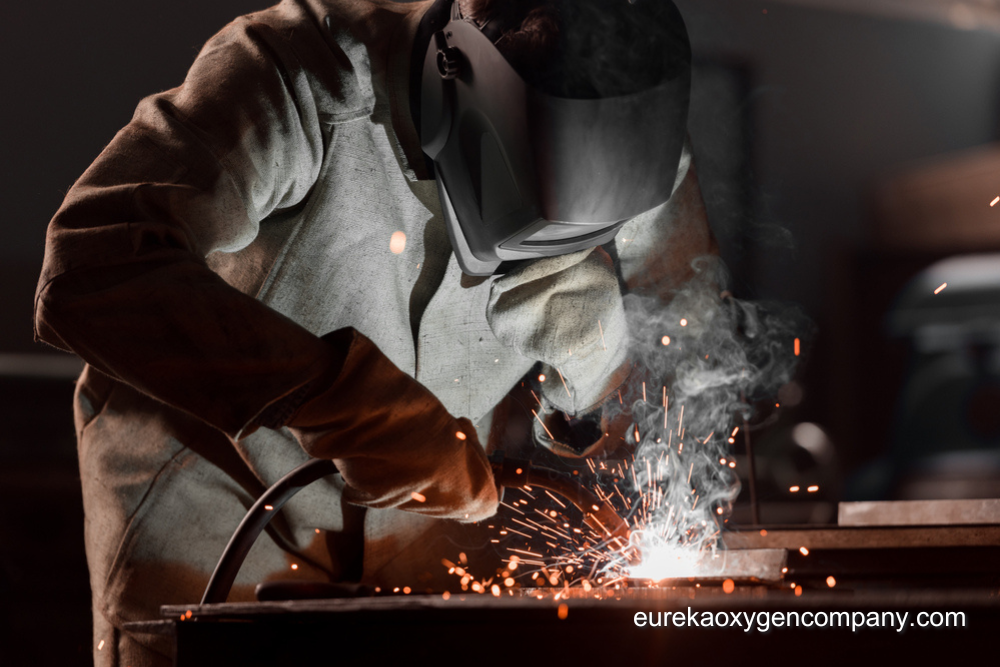
- Causes. The most common cause of cracking is rapid cooling, due to improper welding sequences and techniques. Inappropriate joint design that concentrates stress can also be a contributing factor to cracks.
- Fixes. A great way to prevent this welding imperfection is to preheat the base metal to reduce thermal gradients and minimize cracking. Further, we recommend you use controlled cooling techniques to prevent rapid cooling.
Cold Lap
Cold lap is a type of weld defect that occurs when molten metal does not completely fuse with the cold plate surface, producing a defect similar to cracks that run parallel to the plate. This welding defect can be classified into three types: spatter, overlap, and spatter-overlap cold lap.
- Causes. Cold lap can be caused by low heat input, poor welding techniques, or incorrect travel speed. These factors cause an incomplete fusion between the molten and base metal.
- Fixes. To fix cold lap, increase the heat input to ensure proper fusion of the metals. You can also improve your welding technique by maintaining a consistent travel speed and correct electrode angle.
Undercut
Undercut is a groove melted into the base metal adjacent to the weld, which weakens the joint.
- Causes. Excessive welding speed can cause undercut, as can using an incorrect electrode or torch angle. High welding current is another factor that can lead to excessive melting of the base metal, resulting in undercut.
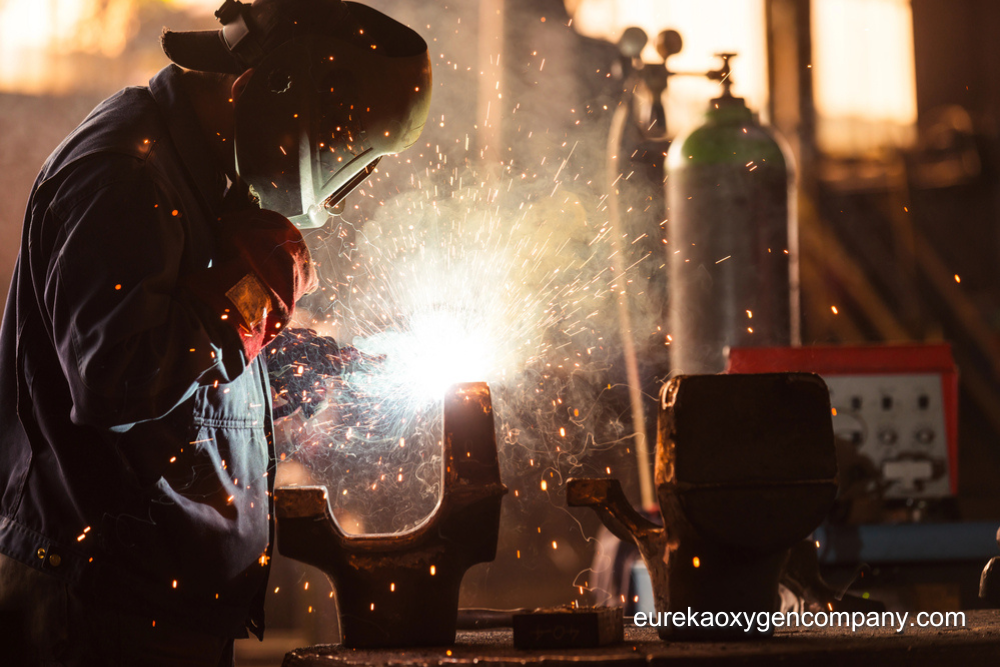
- Fixes. To fix undercut issues, reduce the welding speed to ensure weld beads can be properly formed. Further, adjust the electrode angle for adequate coverage and penetration, and lower the welding current to prevent the base metal from excessively melting.
Incomplete Fusion
Incomplete fusion occurs when the weld metal fails to fuse properly with the base metal or previous weld beads, leading to weak joints.
- Causes. Improper heat input is the number one cause of incomplete fusion, as it prevents the base and weld metal from properly melting. Burn-though is another related issue, where excessive heat input melts through the base metal, creating holes and compromising weld quality.
- Fixes. Increase the heat input by adjusting the welding parameters to ensure complete fusion. To avoid burn-through, carefully control the heat input and monitor the welding process to prevent excessive melting.
Slag Inclusions
Slag inclusions are non-metallic solid materials trapped in the weld metal that lead to weakened weld.
- Causes. This welding problem occurs when the welding area has not been cleaned correctly. The use of incorrect welding parameters and poor welding techniques are two additional causes of slag being trapped in the weld.
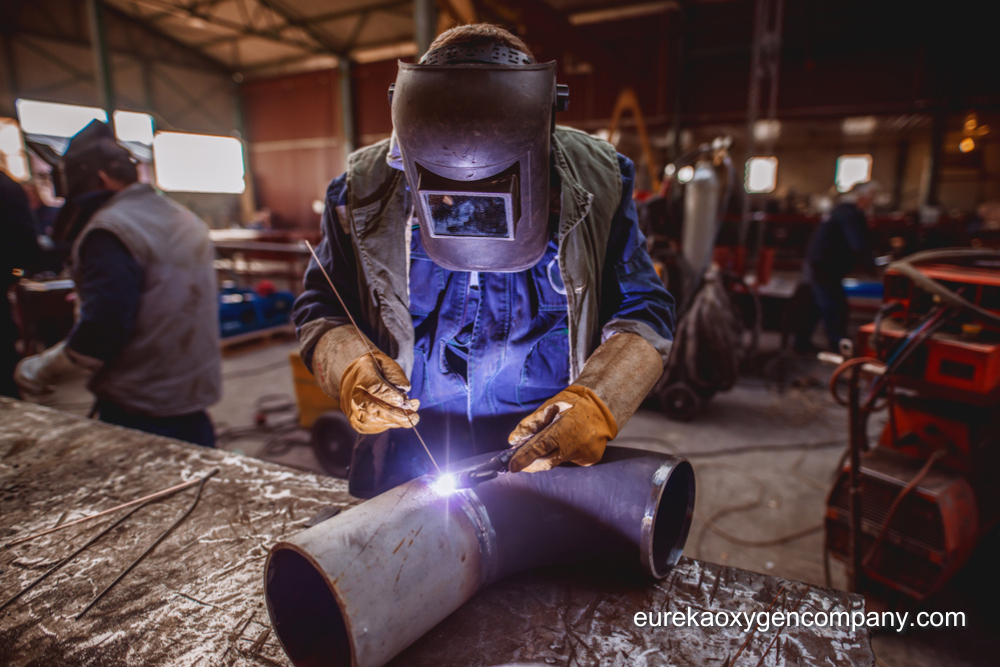
- Fixes. To prevent slag inclusions, clean the weld area thoroughly between passes to remove any slag. Make sure your welding parameters are adjusted correctly to prevent slag entrapment and perfect your welding techniques to avoid trapping slag in the weld.
Final Words
In this post, we talked about the most common welding defects and effective weld repair tips you can implement. At Eureka Oxygen, we believe safety and quality are two of the most important things welders should have in mind, which is why we’re proud to have a robust supply of welding equipment such as PPE and gas cylinders available. We deliver to various areas, and you can access the full list of locations here.