Preventing welding problems has always been challenging. Use our welding tips and tricks to keep your equipment in perfect condition at all times!
Regular maintenance is crucial for keeping your welding equipment running smoothly, ensuring safety and quality work. Neglecting this can lead to equipment failure, compromised safety, and costly downtime.
Summer brings specific challenges for welding operations due to high temperatures that can cause equipment overheating, and humidity that affects both the equipment and the welding process itself.
In this post, we’ll talk about DIY welding maintenance that you can easily conduct that is affordable and ensures excellent results.
Welding Equipment Maintenance Basics: Inspect & Clean
The first thing we recommend you do in this summer welding tips guide is to conduct a thorough inspection of all your equipment. Look for signs of wear and tear, such as cracks in hoses or cables, loose connections, or corrosion on metal parts. Pay close attention to parts that experience the most stress during its use, like the electrode holder, torch, and clamps.
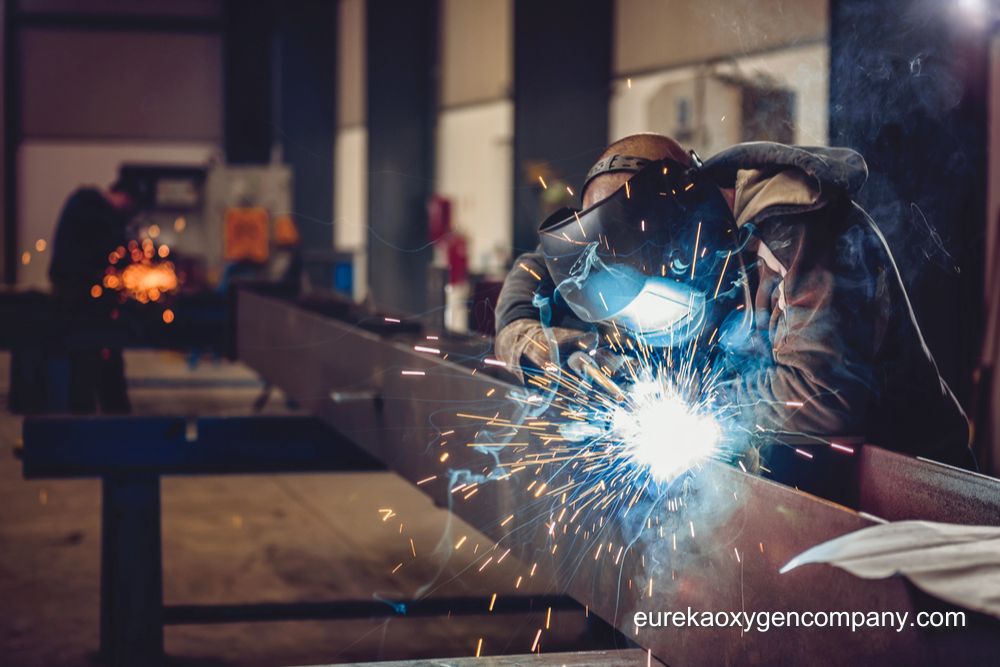
One of the main reasons behind welding equipment care is to address small issues that could become a large problem later, in terms of efficiency, safety, and money.
Regular cleaning is another essential part of keeping your heat and welding equipment in perfect condition. Dust, dirt, and metal particles can accumulate in and around the welding machine, affecting its performance.
To solve this, we recommend you use a soft brush or air compressor to remove debris from vents and internal components. For more stubborn buildup, use a damp cloth with a mild cleaning solution, but avoid using harsh chemicals that could damage the equipment.
Check Coolant Levels and Lubrication
For welding machines with liquid cooling systems, maintaining the correct coolant level is essential, especially in hot weather. Check the coolant reservoir regularly and use the appropriate coolant mixture. Low coolant levels can cause the machine to overheat, leading to equipment failure and potential damage to internal components.

Therefore, for extending welding equipment life, make sure you keep it clean and properly functioning at all times.
As for lubrication, moving parts within the welding machine such as fans, bearings, and motors, require regular lubrication to minimize friction and wear. Over time, lubricants can break down or become contaminated, reducing their effectiveness. Check lubrication points and apply fresh lubricant as needed, following the manufacturer’s recommendations.
Calibrate Your Equipment
Calibration is one of those things that help prevent welding problems that most welders tend to forget about when things are not running smoothly. It ensures that your welding machine delivers constant output in terms of voltage, current, and other parameters. Over time, your equipment can drift out of calibration due to regular use, environmental factors, or aging components.
If you’re looking for easy welding equipment troubleshooting, try calibrating your machine again (and regularly) to maintain the quality of your welds and ensure your machine works within specific parameters.
Gas System Maintenance 101: Gas Flow & Pressure
Consistent gas flow is crucial for shielding the weld pool from atmospheric contamination. Check the flow meter to ensure that the gas flow is within the recommended range for your specific welding process. If the flow is too low or too high, it can lead to poor weld quality, such as porosity or excessive spatter.
Leak detection is another critical point in gas system maintenance, thus gas leaks not only waste valuable resources but also pose significant welding safety risks. After setting the gas flow, use a leak detection solution or soapy water on all connections and hoses and check for leaks. You’ll see bubbles form at the site of any leaks. If you find one, repair or replace the component before going back to work.
Benefits Of Welding Maintenance
Maintaining your welding equipment is essential for safety and efficiency. Regular checks prevent equipment failures that could lead to accidents while ensuring consistent weld quality.
Additionally, staying on top of maintenance minimizes downtime and repair costs, keeping your projects on schedule. By adhering to safety standards through routine supervision, you ensure both compliance and reliability in your welding operations.
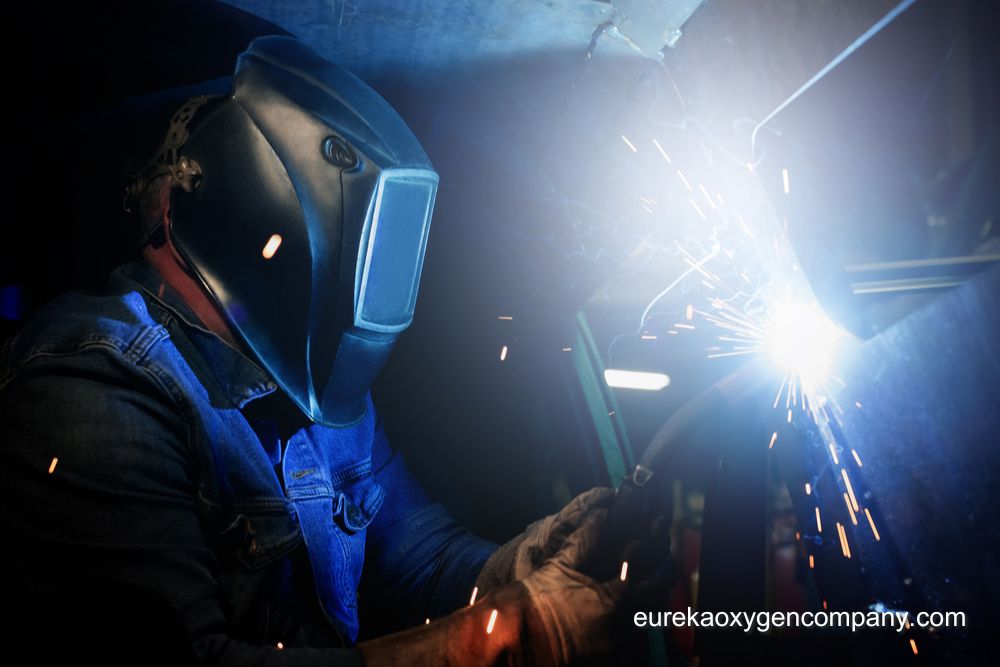
Final Words
Regular maintenance is an investment in the longevity and reliability of your welding equipment. By keeping your gear in top condition, you minimize the risk of unexpected breakdowns, reduce downtime, and ensure that your welds meet the highest quality standards.
At Eureka Oxygen, we want you to strive in your business by providing you with the best welding equipment. Additionally, we deliver cylinder gases, so you don’t have to worry about logistics on top of everything else you have going on. Check our locations to see where you can find us.