Oxygen plays a crucial role in stabilizing the weld pool during the welding process. Its correct use also helps reduce porosity and prevent brittle welds. However, slight adjustments may be necessary in cold weather to achieve the right balance, ensuring that the arc is stable and can create a strong bond.
Let’s discuss the role of oxygen in cold weather and what you can do to prevent common issues.
How Cold Weather Affects Oxygen and Gas Behavior
Oxygen is a key component in welding, especially when paired with acetylene or other fuel gasses. In cold weather, however, gas behavior can shift in response to temperature changes. Cold temperatures reduce gas pressure in tanks, making achieving a consistent flow rate more difficult. This can cause fluctuations in flame stability, leading to incomplete welds, increased spatter, or even safety risks.
To prevent these issues, it’s crucial to understand cold weather gas behavior and how to adjust your equipment setting to maintain control over the welding process.

Understanding Oxygen’s Role in Weld Pool Stability
Oxygen plays a crucial role in stabilizing the weld pool during welding. In colder conditions, achieving the right level of penetration and fusion can be challenging. Since metal reacts differently at lower temperatures, the introduction of oxygen affects both the weld pool’s temperature and the arc’s stability.
Using oxygen correctly helps maintain a consistent weld pool, reducing porosity, and preventing brittle welds. However, slight adjustments may be necessary in cold weather to achieve the right balance, ensuring that the arc is stable and can create a strong bond.
Adjusting Oxygen Flow and Pressure for Winter
Since oxygen and other gases become denser in cold weather, the flow rate can vary if not properly adjusted. Oxy-fuel welding processes, for example, require a consistent oxygen supply to produce clean and efficient welds. In freezing temperatures, you may need to adjust regulators and pressure settings to maintain a desired flow rate.
You can also work with your industrial gas supplier to adjust settings for winter conditions.
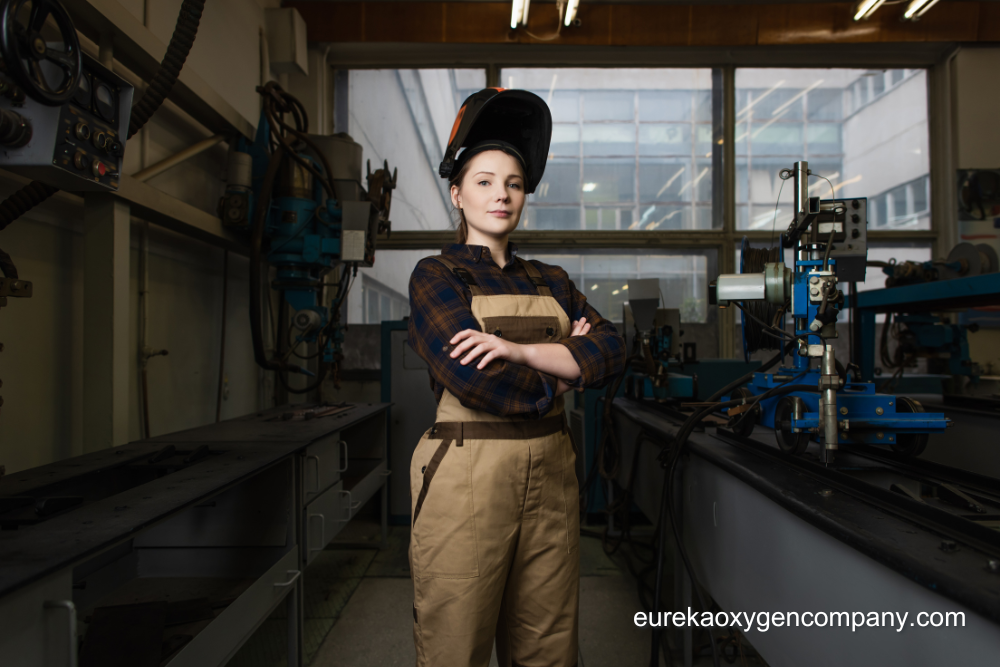
Storing Oxygen Tanks in Cold Weather
Proper storage of oxygen tanks is essential to ensure their safe and efficient use during winter. When oxygen tanks are exposed to cold, the gas pressure drops, and the materials surrounding them (like seals and valves) may become brittle, increasing the risk of leaks or breaks.
Store oxygen tanks and other gas cylinders in a temperature-controlled area, especially overnight. If you cannot do this, consider at least using insulated covers or wraps to reduce the impact of low temperatures. Be sure to follow cold weather equipment prep guidelines to keep gas tanks in good condition.
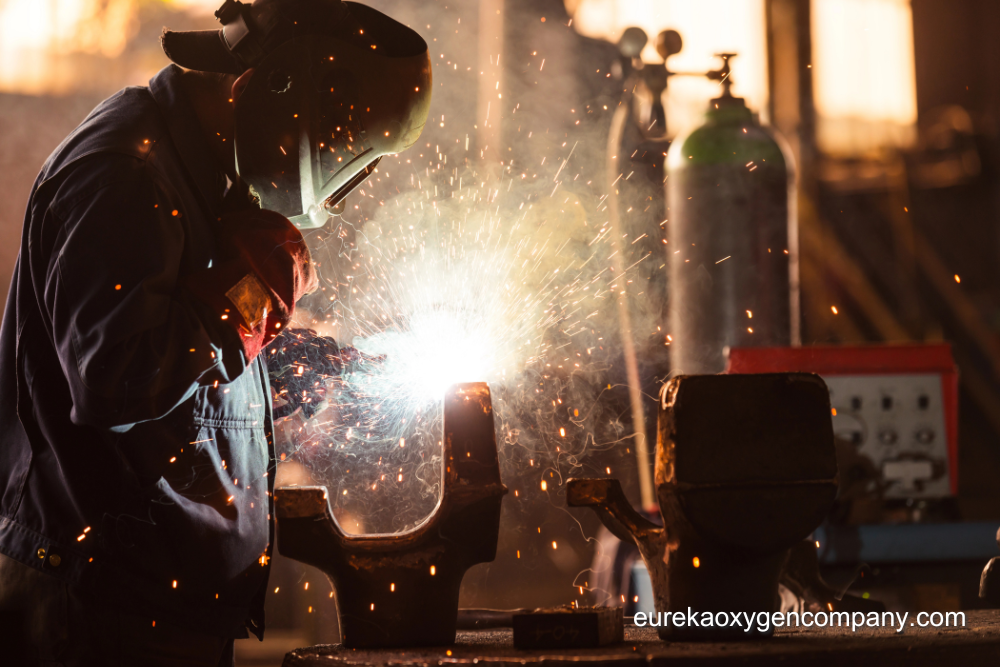
Safety Considerations for Using Oxygen in Low Temperatures
Using oxygen in welding always requires caution, and the risks increase even more in cold weather. Cold metals are more prone to fracturing, and lower temperatures can lead to gas leaks from cracked hoses or damaged connections. Additionally, any build-up of oxygen in an enclosed space can increase the fire risk.
This is why having appropriate fire suppression equipment and services on-site is essential for managing the risks. Inspect fire extinguishers, fire blankets, and other fire suppression tools regularly to ensure they’re in good working condition. Cold weather can affect fire suppression materials, so ensure these tools are properly winterized as part of your safety protocol.
Visit Eureka Oxygen
Understanding the unique behaviors of oxygen in cold weather can help you adjust your welding practices accordingly, maintaining weld quality and minimizing safety risks.
Count Eureka Oxygen as your reliable industrial gas supplier for all your welding needs, from welding supplies and equipment to high-quality cylinder gases. Explore our locations and delivery areas to see how we can support your operations with timely, local service.
Preventing Oxidation and Metal Brittleness in Winter Welding
One of the main concerns with oxygen use in welding, especially in cold weather, is the potential for excessive oxidation. Cold metal surfaces are more susceptible to rapid cooling, which can lead to brittleness and an increase in the risk of oxidation.
To counter this, monitoring the oxygen flow rate and, where possible, using a controlled environment for the welding area is essential. A slight reduction in oxygen flow can sometimes prevent over-oxidation and reduce metal brittleness in colder conditions, ultimately enhancing weld quality.