Making informed choices for efficient welding operations
In the diverse landscape of industrial equipment and welding techniques, two prominent methods have emerged as steadfast pillars of metal joining: gas welding and electric welding.
These techniques offer distinct advantages and drawbacks, catering to the diverse needs of industries ranging from construction and manufacturing to artistry and fabrication. Understanding the intricacies of each method is essential in making informed decisions for your welding processes, ensuring that projects are executed with precision, efficiency, and the highest quality.
In this post, we cover all the pros and cons you should know about gas welding and electric welding.
Gas Welding: The Time-Tested Craftsmanship
Gas welding, an age-old technique steeped in tradition, has stood the test of time as a symbol of precision and artistry in the world of metal joining. This method, also known as oxy-fuel welding, relies on the controlled combustion of gases to produce a flame that welders deftly manipulate to achieve intricate welds.
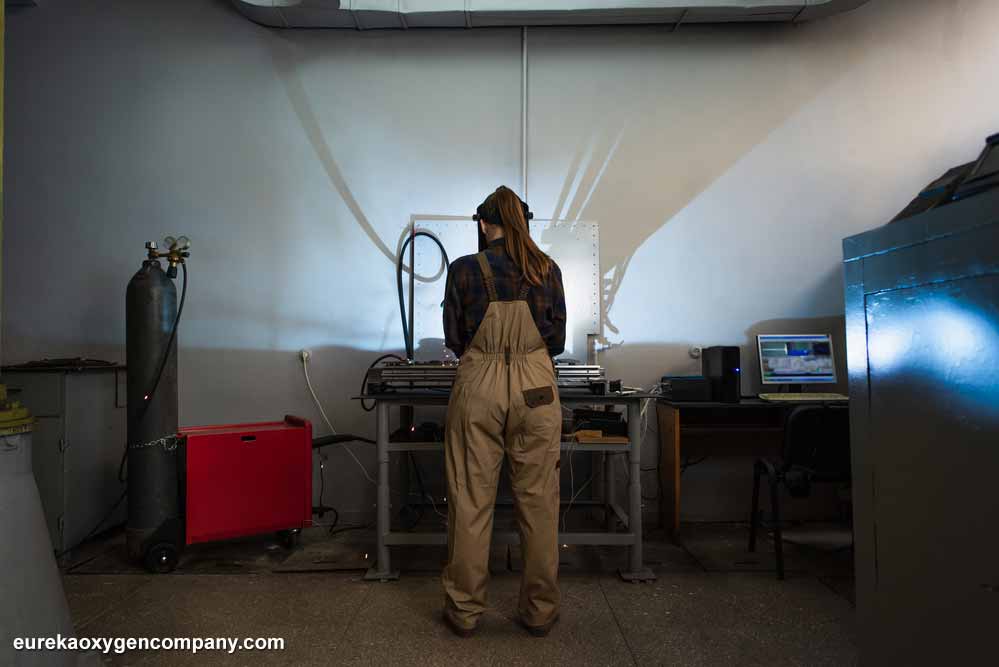
Pros of gas welding:
- Precision and Craftsmanship: Gas welding embodies a time-honored tradition of precision and craftsmanship. This method relies on the controlled combustion of gases, most commonly acetylene, hydrogen, and propane, mixed with oxygen to produce a precisely adjustable flame. This precision is particularly valuable for applications demanding intricate detail and finesse, such as ornamental ironwork, artistry, and jewelry making.
- Flexibility with Industrial Gases: The versatility of gas welding stems from the assortment of industrial gases available for use. By carefully selecting the gas mixtures, welders can fine-tune the characteristics of the flame, allowing for optimal performance on various materials and thicknesses.
- Low Heat Input and Heat-Affected Zone (HAZ): Gas welding’s relatively low heat input is advantageous for projects involving thinner materials. The controlled flame minimizes the size of the heat-affected zone (HAZ), where the material’s properties change due to elevated temperatures. This is crucial when working with delicate metals or components that cannot withstand excessive heat, ensuring the integrity of the material.
Cons of this welding method
- Limited Application for Thicker Materials: While gas welding excels in precision and detail, its lower heat output limits its suitability for thicker materials. For heavy-duty welding tasks, electric welding methods such as MIG and TIG welding are often preferred due to their higher heat input.
- Slower Welding Speed: Gas welding can be relatively slower when compared to electric welding methods. The manual nature of gas welding, which involves controlling the torch and filler rod simultaneously, can result in a slower welding speed. This can be a drawback for projects that demand high-volume production and faster completion times.
Electric Welding: The Power of Current
Electric welding, a dynamic set of techniques fueled by the power of electricity, has revolutionized the world of metal joining through its adaptability and efficiency. Techniques like MIG (Metal Inert Gas) welding and TIG (Tungsten Inert Gas) welding utilize electrical currents to generate intense heat, melting metals and creating strong, reliable welds.
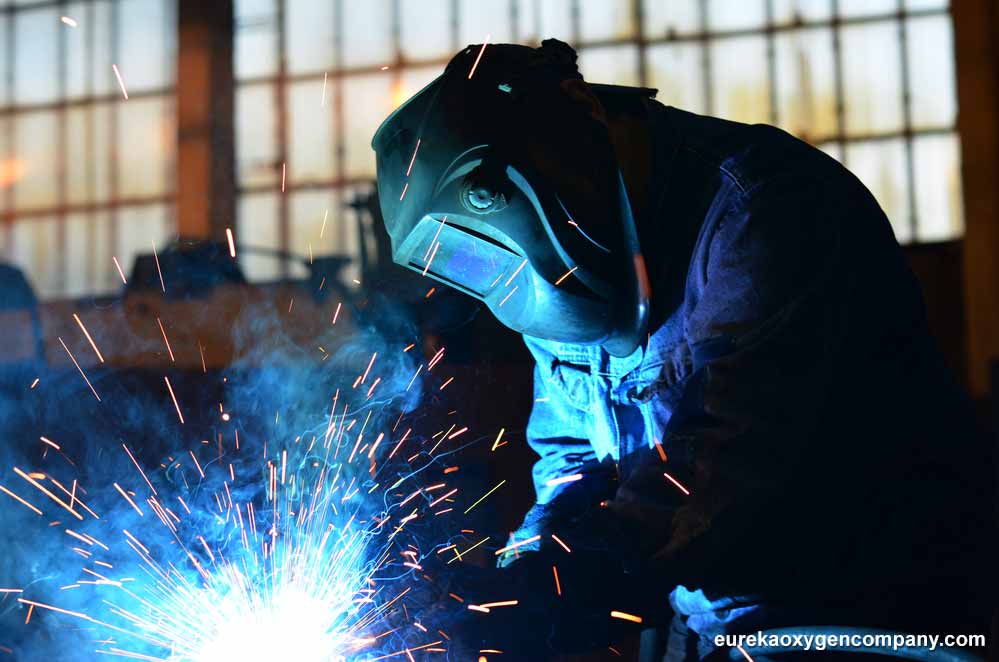
Pros of electric welding
- Adaptability to Different Materials: Electric welding methods exhibit exceptional versatility. They can be employed on a wide array of materials, spanning from common metals like steel and aluminum to specialized alloys such as stainless steel. This adaptability makes electric welding methods suitable for diverse industrial applications.
- Enhanced Welding Speed: Electric welding methods, owing to their higher heat input and greater deposition rates, often offer quicker welding speeds compared to gas welding. This rapidity makes them well-suited for projects necessitating efficient production rates without compromising on weld quality.
- Cleaner Welds with Inert gases: Electric welding methods commonly utilize inert gases, including argon, carbon dioxide, and helium, to shield the weld pool from atmospheric contamination during the welding process. This shielding effect prevents oxidation and other detrimental interactions, resulting in cleaner and stronger welds. The need for extensive post-weld cleaning is reduced, streamlining the workflow and saving valuable time.
Cons of electric welding
- Complex Equipment Setup: One of the trade-offs with electric welding methods is the relatively complex equipment setup they require. These methods involve power sources, wire feeders, and additional components that contribute to a more intricate arrangement compared to the simplicity of gas welding equipment.
- Limited Precision for Certain Applications: While electric welding methods provide exceptional efficiency and versatility, achieving the same level of precision and delicacy as gas welding in projects demanding intricate artistic work can be challenging. Gas welding’s torch manipulation allows for a higher degree of control in such scenarios.
Choosing Wisely: Finding the Balance
Selecting the appropriate welding method between gas welding and electric welding hinges on comprehending your project’s specific demands. If your goal revolves around meticulous craftsmanship and intricate detailing, gas welding holds a clear advantage. However, when you’re working with thicker materials and require rapid production rates, electric welding methods often become the preferred choice.
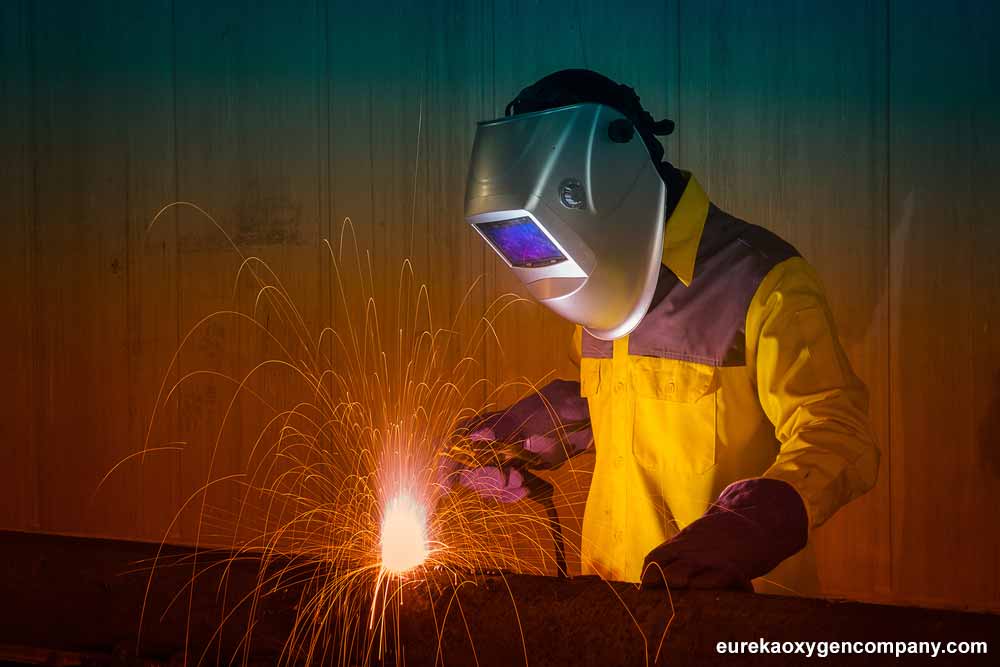
Furthermore, the selection of industrial gases plays an instrumental role in welding success. In electric welding, the use of inert gases like argon, carbon dioxide, and helium ensures that the weld pool remains shielded from the atmosphere, contributing to the weld’s cleanliness and strength. In gas welding, the judicious combination of gases with oxygen determines the flame’s characteristics and heat output, enabling precise control over the welding process.
About Eureka Oxygen
In the realm of industrial innovation and progress, few companies stand as prominently as Eureka Oxygen. With a steadfast commitment to excellence and a constant dedication to empowering various industries, Eureka Oxygen has become a trustable partner in the world of specialty gases.
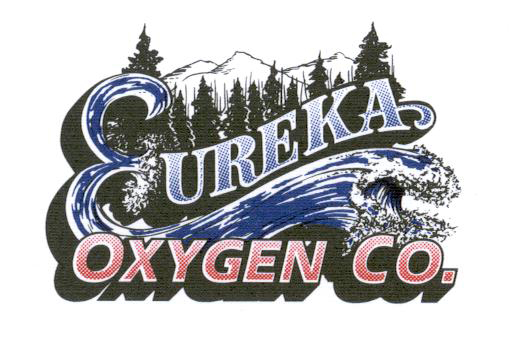
At the heart of our mission lies the provision of high-quality gases and comprehensive solutions that drive efficiency, safety, and precision across diverse industrial processes.
Take a look at our products, and the locations we serve, and don’t hesitate to contact us with any inquiry you might have.