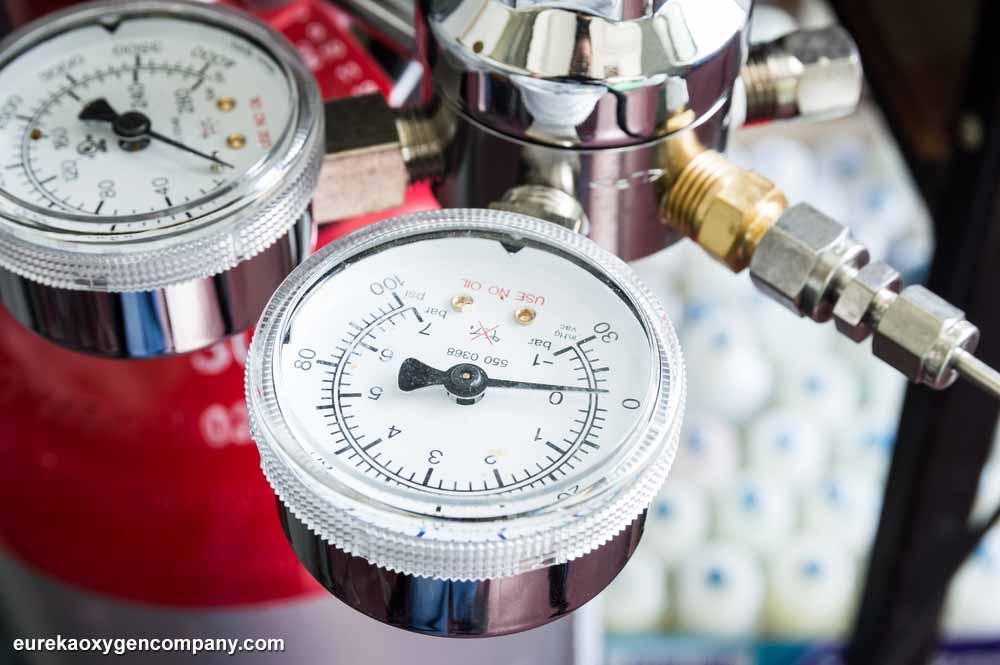
That conversion can either be accomplished in one step, which provides a less stable or constant pressure. In these single-stage regulator operations, the output pressure must be manually adjusted to maintain the required specific pressure for the welding operation at hand. As the pressure in the cylinder drops (as the gas inside is depleted), the output pressure rises conversely and must be manually reduced with the regulator. A two-stage regulator, as its name indicates, accomplishes this pressure reduction in two steps.
The first step (conducted in the first-stage regulator) reduces that 200-300 bar pressure to a steady 10-bar pressure in a non-adjustable process.
The second stage is then used to adjust that 10-bar flow to the precise pressure and flow required for the welding task being performed.
A third, less commonly mentioned, form of regulator is the flow meter regulator, which is essentially a two-stage regulator. This regulator’s second stage is replaced by the flow meter, which controls flow rather than pressure – as measured in SCFH (Standard Cubic Feet per Hour). The flow meter is typically chosen for TIG and MIG applications.
While this may seem initially boggling, the selection of the most appropriate regulator for your intended application can be determined by a simple matrix, based on the component factors that must be considered.
Those factors are
- (a) gas type (discussed above)
- (b) application (whether high-pressure for oxy-fuel applications or low, controlled pressure for TIG , (for example)
- (c) gas flow rate (a related but distinct factor from pressure)
- (d) equipment compatibility (the gas-to-regulator correspondence mentioned earlier but also similar compatibility for all torches, hoses, and fitting)
- (e) safety considerations and manufacturer’s recommendations.
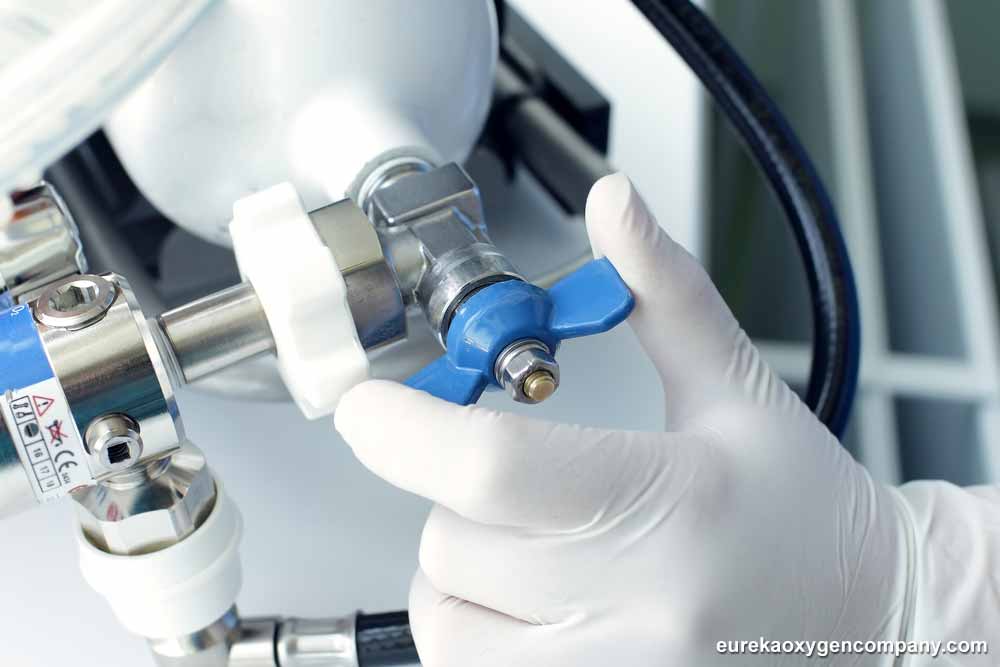
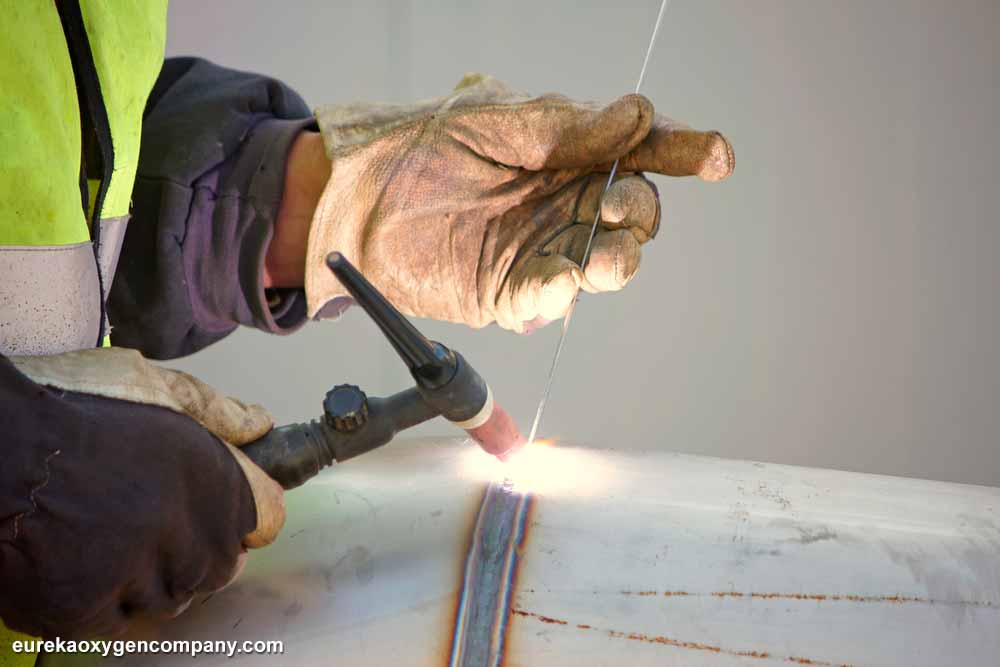
The relatively simple matrix is as follows:
Suitable Welding Applications | Regulator Type |
---|---|
Cutting, brazing | Single-stage |
TIG, MIG | Dual-stage |
Oxy-fuel welding | High-pressure |
MIG, TIG | Low-pressure |
Exotic or highly reactive gases, specialized applications | Specialty |