Industrial gases like oxygen, acetylene, argon, and nitrogen are essential for crucial processes like metal fabrication, chemical production, food freezing, and healthcare. But what allows these gases to be portable, storable, and usable? The answer lies in the science of gas compression and expansion. Understanding these principles helps ensure that gases are handled safely and efficiently. This article provides an overview of the physics involved and why gas compression is critical for industrial gas applications.
Gas Laws
The gas laws explain the behavior of gases, sets of mathematical formulas relating pressure, volume, temperature, and amount. Boyle’s law states that pressure is inversely proportional to volume for a fixed amount of gas at a constant temperature. As volume decreases with compression, pressure rises. Charles’ law says that volume is directly proportional to temperature, so gases expand when heated. The Ideal Gas Law combines these principles, relating gas pressure, volume, amount, and temperature. By manipulating these variables, gases can be compressed or expanded.
Adiabatic Compression
One method of gas compression is adiabatic compression. No heat transfers into or out of the gas during this process. Mechanically decreasing the container volume causes the gas pressure to rise rapidly. This conversion of mechanical work into internal energy raises the gas temperature.
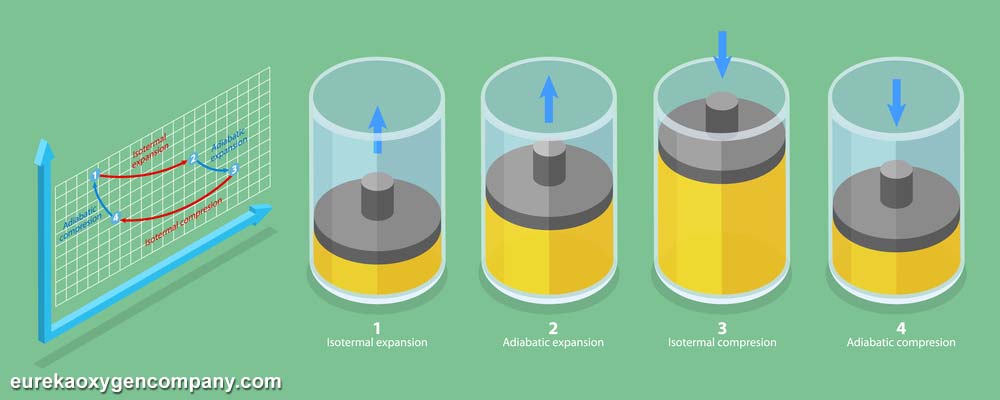
However, there is no heat exchange to lower this temperature spike with the surroundings. Due to the increasing temperature, the process follows a curve on the pressure-volume diagram.
Isothermal Compression
Isothermal compression involves compressing gas while keeping the temperature constant. This requires removing heat as mechanical work raises the internal energy and temperature. Holding a significant heat transfer rate out of the gas maintains an isothermal process at a steady temperature. The ideal process follows a hyperbolic curve on the diagram, producing higher pressures for lower volumes while staying at the same temperature.
Reaching proper isothermal compression is challenging in reality. However, using multiple stages with cooling between stages can approximate constant-temperature conditions. This prevents overly high temperatures that lower compressor efficiency and require stronger materials.
Gas Expansion
The reverse of compression is gas expansion. This lowers pressure as gases occupy larger volumes, following the same gas laws. Expansion cools gases like nitrogen and argon until they liquefy for storage in portable cylinders. Lower-pressure gases then vaporize as they exit the cylinder and expand. Carefully controlling flows prevents damage from expanding gases, cooling, and condensing moisture inside regulators or lines.
Cylinder Design
Gas cylinder strength resists the high internal pressures produced by compression. At up to 2400 psi, cylinder pressures can be hundreds of times higher than ambient levels. Thick, seamless steel or aluminum construction contains these forces. But cylinders must also be lightweight enough to transport. So, dimensions follow standards for size, capacity, and pressure levels for each gas type. Valves rated for the design pressure control flow out of the cylinder during use.
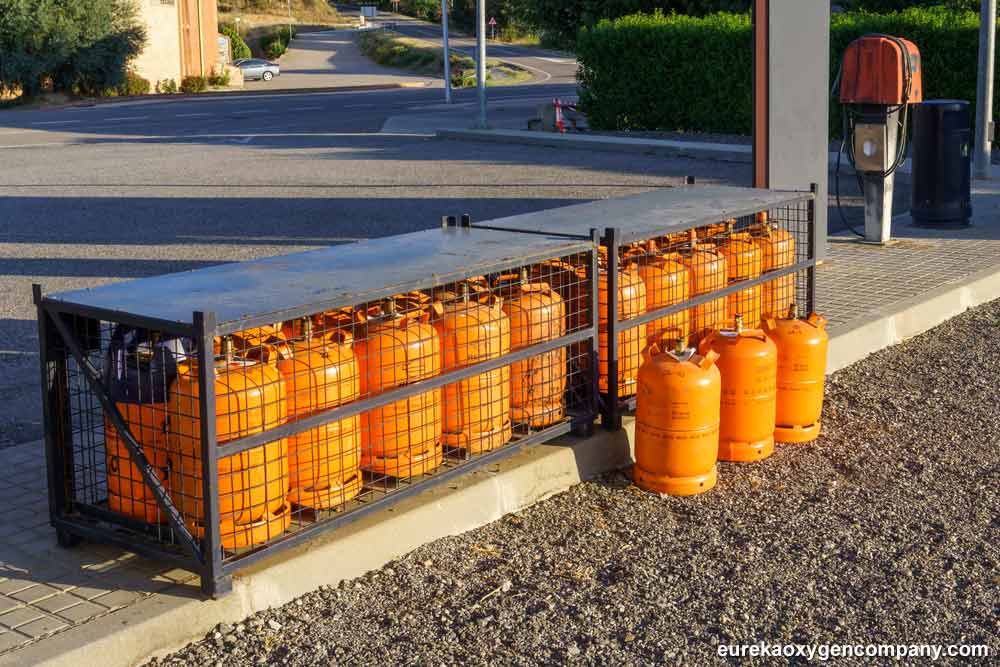
Compression Hazards
Rapid compression of gases generates heat that could ignite flammables like acetylene or hydrogen. Oxygen gas also accelerates combustion. Excessive pressure may rupture containment vessels if equipment fails or the temperature rises too high. Compressed gases can explode if heated past safe limits. Storage areas must isolate incompatible gases and incorporate ventilation, explosion-proof electrics, and fire prevention systems.
Proper staff training in cylinder handling minimizes compression hazards. Safety devices like pressure relief valves vent excessive pressure buildup. Following manufacturer filling procedures and marked service pressures prevents overfilling cylinders. With responsible filling and maintenance by suppliers, gases stay compressed until expanded for use.
Putting Gas Compression to Work
Understanding gas behavior allows compression for economical use in welding, chemical processes, manufacturing, food service, and healthcare. Compressed into portable cylinders, utility carts, or bulk tanks, compressed gases provide an easily tapped source of chemicals essential to modern industries. Just follow all safety measures and procedures when handling these pressurized vessels. And rely on professional gas suppliers to properly compress, fill, and certify cylinders for the pressures your applications require. By leveraging the science of gas compression and handling cylinders responsibly, businesses ensure ready access to the gases they need.
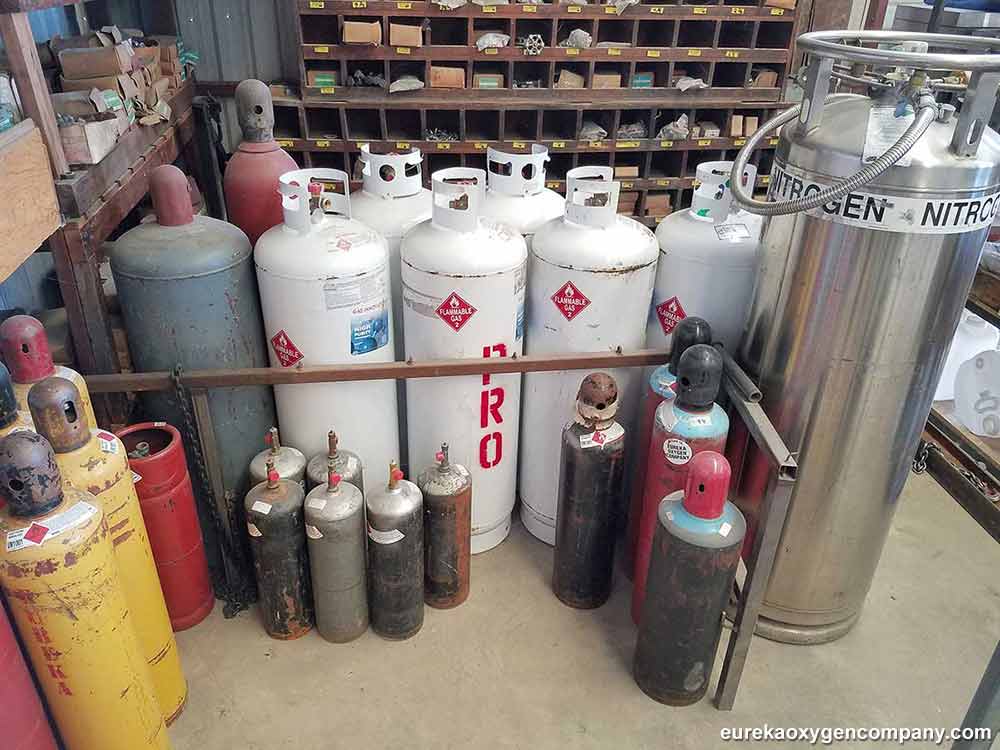
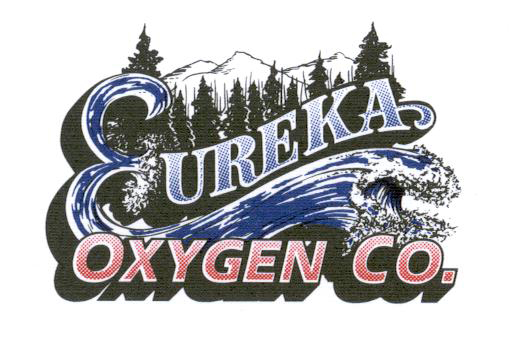