Welding best practices for taking care of your equipment to increase efficiency and reduce potential safety risks
Proper maintenance of welding equipment is essential to ensure the efficiency, safety, and longevity of your tools. Not caring for your equipment can negatively impact welding safety and quickly become a threat, apart from increasing operational costs.
Establishing a proper maintenance routine allows you to enhance your tool’s performance, extend the lifespan of your tools, as well as deliver your work on time (if not sooner). Just as you spend time putting on all your PPE clothing and being extra careful with potential fire risks, you should look after your tools.
Welding Equipment Maintenance Guide
In this section, we will explore the key aspects of general maintenance, including regular cleaning routines, strategic storage considerations, and more. These preventative maintenance guidelines help preserve your equipment and enhance safety in the workplace.
- Clean regularly. Get rid of the dust, debris, and spatter using some compressed air, soft brushes, and the right cleaning stuff to ensure their proper functioning.
- Store properly. Keep your welding equipment in a dry, well-ventilated location, ensuring coverage when not in use. This prevents your tools from getting in contact with the environment, which can start to corrode them over time.
- Inspect frequently. Regularly inspect cables, hoses, connections, and others for signs of wear, tear, damage, or leaks.
- Follow the manufacturer’s recommendations. Consult the manufacturer’s manual for specific guidelines on cleaning, lubrication, and calibration measures. The recommendations in the manual align with the equipment’s design and specifications, making it easier to look after.
Specific Safety Gear Maintenance: Tips for Different Equipment
Each tool in metalworking requires slightly different care routines to ensure they’re working properly and don’t present a threat. Below, you can find a brief guide about different care tips you can start implementing to prolong your welding equipment lifespan.
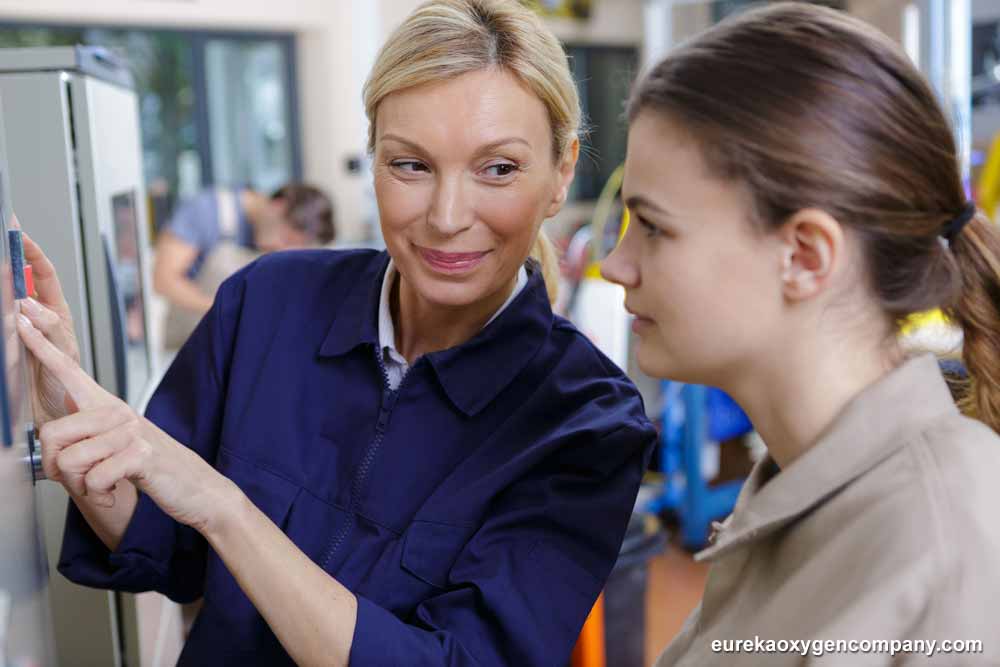
Welding Machine Maintenance
A welding machine is by far one of the most important tools you can have in your workplace, and its longevity depends on meticulous care. In addition to regular internal cleaning to prevent overheating, consider inspecting and cleaning cooling systems. Overheating not only compromises performance but can lead to long-term damage.
Monitoring gas pressure is equally crucial, ensuring a steady and efficient welding process. Regular checks on these elements contribute to the sustained reliability and optimal functioning of your welding machine.
Essentially, you should:
- Conduct regular internal cleaning to prevent overheating.
- Monitor and maintain the cooling systems to sustain optimal temperature.
- Regularly check gas pressure levels for consistent and efficient welding.
Welding Torch Maintenance
Apart from ensuring clean nozzles for a precise and stable flame, attention to electrode holders is essential. Regular inspections will identify signs of wear, allowing timely replacement and preventing disruptions to your welding process. Periodically replacing worn tips and liners is a simple yet effective step to maintain the quality of your welds, ensuring precision and efficiency in every project.
Don’t forget to:
- Ensure clean nozzles for precise and stable flame performance.
- Check electrode holders for signs of wear and replace them if needed.
- Regularly replace worn tips and liners to ensure welding quality.
Grinding Equipment Maintenance
The maintenance of grinding equipment directly influences its performance when preparing surfaces. Frequently changing grinding discs is necessary to ensure efficiency, as well as maintaining dust collectors to prevent clogs.
Proper ventilation contributes to the longevity of the equipment as well as eliminates risks associated with airborne particles, creating a safer workplace.
Make sure you’re:
- Consistently changing your grinding discs.
- Maintaining dust collectors to prevent clogs and enhance performance.
- Prioritize proper ventilation to mitigate risks associated with airborne particles.
Safety Gear Maintenance
Regularly cleaning and inspecting helmets, gloves, and respirators for signs of damage or wear is a great measure to ensure they function effectively when needed most. Immediate replacement of any compromised or damaged safety gear is critical, as it directly correlates to the well-being of the welder. This diligence in safety gear maintenance is not just a regulatory requirement, but a commitment to creating a secure and protected workspace.
Always:
- Regularly clean and inspect helmets, gloves, and respirators for signs of damage or wear.
- Promptly replace any compromised or damaged safety gear.
Final Words
In this post, we talked about the best welding equipment maintenance tips and practices you should implement regularly to ensure all your tools are working properly and that they don’t present a threat to other employees and your workplace.
Eureka Oxygen has a robust supply of safety products, welding equipment, and industrial and cylinder gases like butane, propane, dry ice, and more, which you can browse here. We serve a wide range of locations, from the Golden Gate Bridge to Gold Beach, OR, so no matter where you are, we can deliver your products safely and on time.