There are a number of key factors which guarantee top-quality welds. These include patience, top-notch equipment, and ideal weather conditions. Conducting welding operations during the colder months of the year requires consideration of certain precautions and conditions, which can affect the quality of your welds.
Exposure to extremely low temperatures will make your welds cool off much quicker than usual, triggering cracking and poor penetration. Also, the difference in heat levels between your workpieces and the welds may trigger extreme warping. It is wise to consider how cold weather can adversely affect welding equipment and what you can do to counteract it.
The effects of cold weather on welding equipment
Freezing weather conditions are known to negatively impact welding equipment if precautions aren’t taken. Like all electronic equipment, welders and welding equipment can only be used safely in dry and warm conditions. However, the finest welding equipment is engineered to withstand operation in extremely cold weather. It is in fact moisture and dirt that you want to be cautious of when performing winter welding jobs.
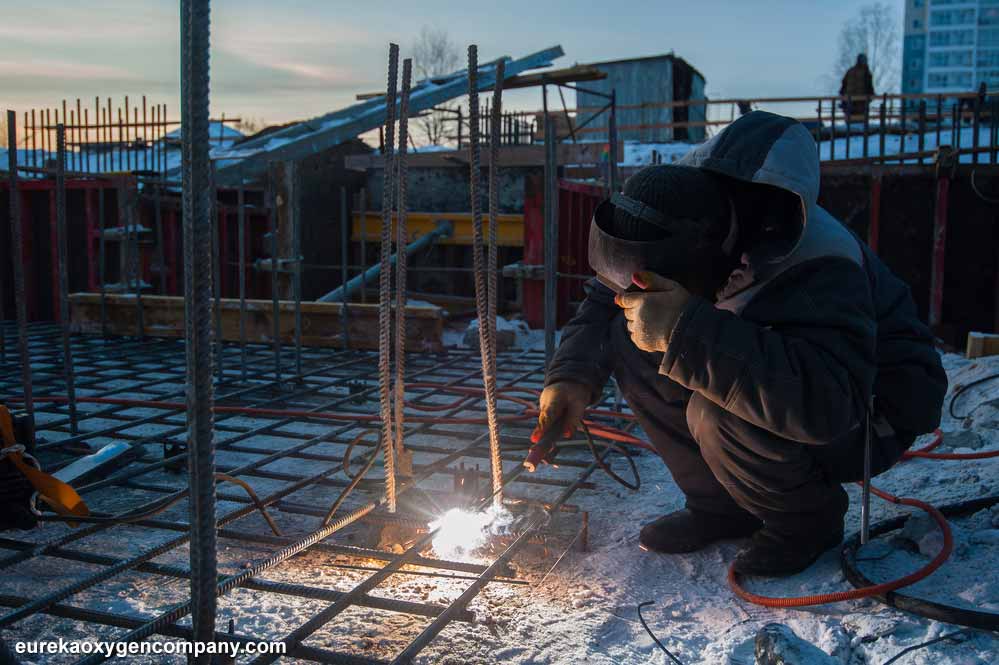
As for dirt, it is prudent not to leave your welder uncovered when it’s not in use to prevent exposure to dirt and grime which is blown around by winter storms. You should always make sure you invest in a decent cover for your welding equipment, which will keep elements like snow, sleet, and rain from impairing your equipment.
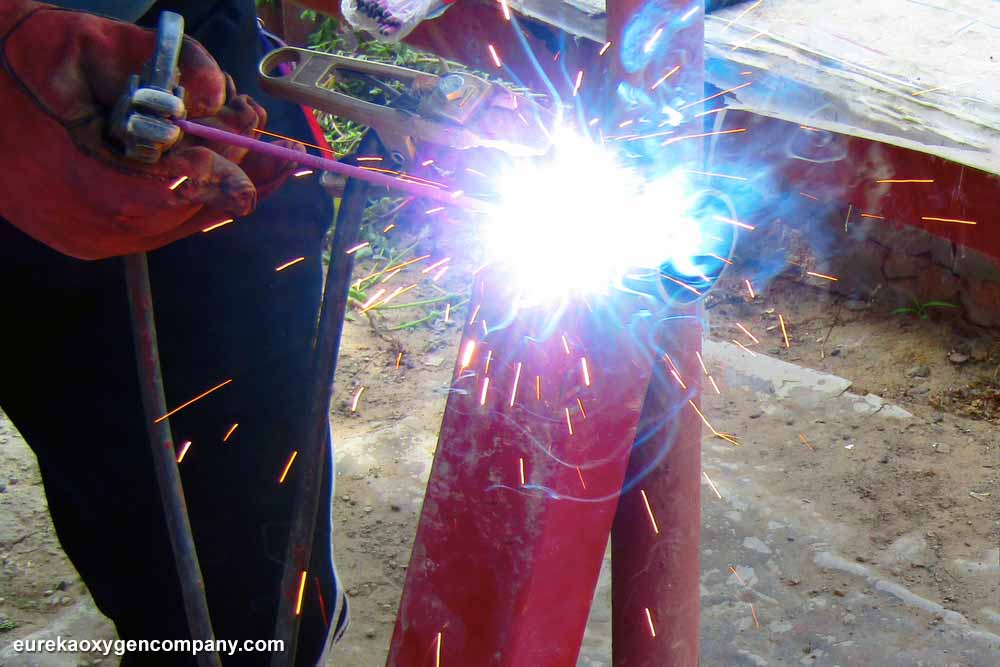
Always ensure your welding rods are warm and dry
Stick welding is often the welding technique of choice for most welders during wet and cold weather conditions. This is mainly because it offers the best solution in terms of working on thicker metals during inclement weather. Stick welding is noted for being both simple and robust. However, during winter, electrodes and welding rods require special attention.
When welding rods get wet, the arc’s heat will cause the external shielding layers to crack and even fall off during the welding operation. Also, when water vapor comes into contact with the arc’s high heat, it will trigger contamination of your welds. A good solution to ensure your welding rods are always dry and warm is investing in a portable rod oven.
Always preheat your workpieces
Poor weld penetration between two base metals almost always triggers weld failure. It is highly advisable to preheat your workpieces to promote good penetration. When left in a cold state, base metals will tend to serve as heat sinks that draw out the heat of your welds. When your welds cool off too quickly, they will be more prone to crack. Ideally, it is recommended to preheat your thicker workpieces to a temperature of around 50oF prior to commencing your welds. You may use either a propane or oxy-acetylene torch to preheat your base metals.
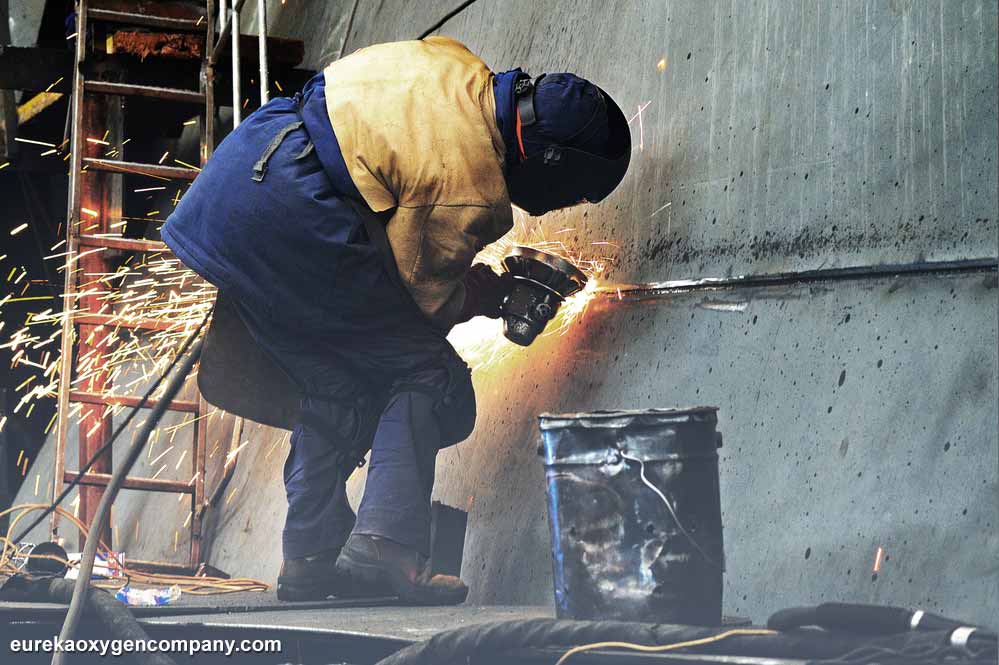
Keep warm and safe to maintain your welding focus
Welding is a manual process that demands plenty of concentration and skill. When you are cold, your concentration can be significantly impaired. You will need to wear layers of clothing to keep yourself warm and also ensure that the outer clothing is flame-retardant. You should don heavy-duty welding gloves to help keep your fingers warm so they articulate well.