Mild steel is an alloy of iron and carbon, with a carbon content of approximately 0.16 to 0.29. It is known to possess a relatively high melting point of up to 1520oC. This given melting point makes mild steel have a high ductility the moment it is heated. In turn, this makes it especially ideal for diverse welding applications. This kind of carbon steel is to be had in a wide variety of forms. This includes sheets, tubes, telescopic tubes, box sections, pipes, t sections, angles to name but a few.
Mild steel is arguably the easiest kind of metal to weld in numerous different applications. The lower the carbon content, the easier it is to weld steel and mild steel fits this bill to the T. Also, low carbon mild steel happens to be the industry gold standard when it comes to room temperature welding applications. It is also one of the least expensive welding metals to be had in the market. All these properties make mild steel particularly beginner-friendly. Let us now take a closer look at the best method and equipment you can use in welding mild steel for beginners.
What is the best beginner-friendly welding process and equipment for mild steel?
For a beginner, the very best welding method for mild steel is MIG welding. It is also very popular with DIY hobbyists because it delivers the cleanest finish when working with mild steel. MIG welding also permits welders to create diverse sorts of fabrications together with maintenance welds of mild steel with the greatest ease. In MIG welding, a continuous solid wire is fed through the welding gun towards the weld puddle and eventually joins two or more base materials together.
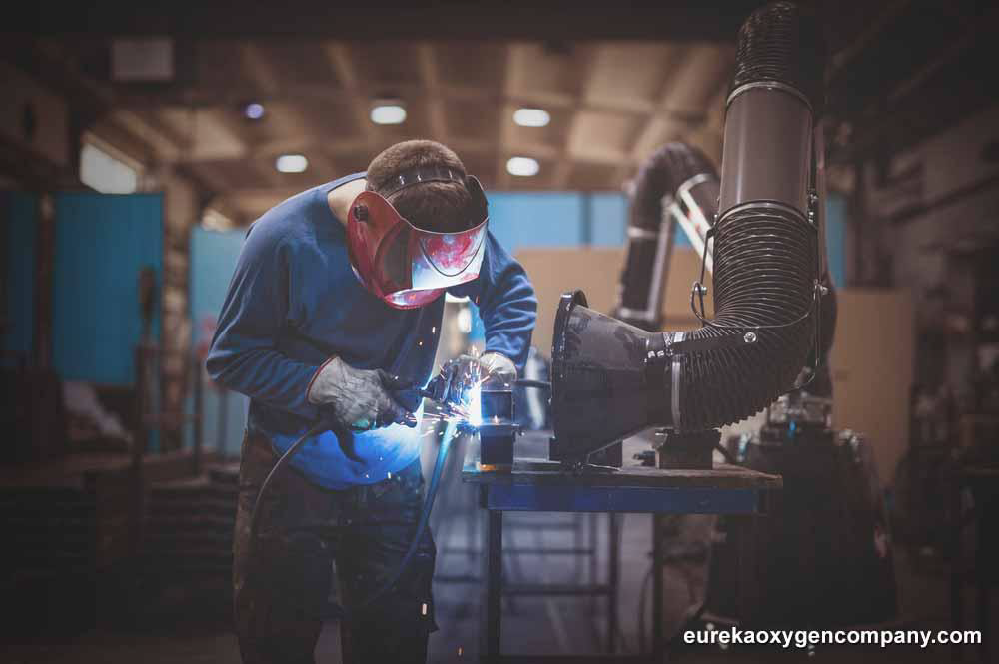
Also, a shielding gas is simultaneously channeled through the welding gun to offer adequate protection against any contamination of the weld pool. Apart from its unmatched flexibility and versatility, MIG welding is noted for being easy to learn and master since the electrode is fed automatically. This enables the welder to concentrate totally on the welding gun and the material. Let us now look at the main components of equipment used to weld mild steel by the MIG welding method.
The power source (MIG welder)
MIG welders operate on the DC current which provides a flat and constant voltage. The exact welding current to use at any particular time is determined by the wire feed speed, while the arc length is determined by the voltage level. In MIG welding mild steel, the wire burn-off rate is seamlessly adjusted automatically to compensate for slight variations in three main variables. These are the distance between the gun and the workpiece, the wire feed speed, and the current pickup rate. MIG welding utilizes three different modes of metal transfer, which are pulsed, spray and dip. For thin section metals such as mild steel, a low welding current is made use of.
Wire feed system
To provide stability and reproducibility, MIG welding depends on the performance of the wire feed system. The wire needs to be fed smoothly, and the welder needs to keep close attention on the feed rolls and liners. There are three different wire systems used in MIG welding. These are pinch rolls, push-pull, and spool-on-gun.
Conduit
The conduit utilized in MIG welding tends to have a length of at least 5mm. To facilitate proper wire feeding, this component should be kept short and straight all the time.
Welding gun
The welding gun in MIG welding serves a number of essential functions. To begin with, it directs the wire to the joints. Secondly, it transfers the current to the wire, and thirdly, it relays the shielding gas to protect the weld puddle. For welding mild steel, the air-cooled welding gun variety is suitable for beginners.
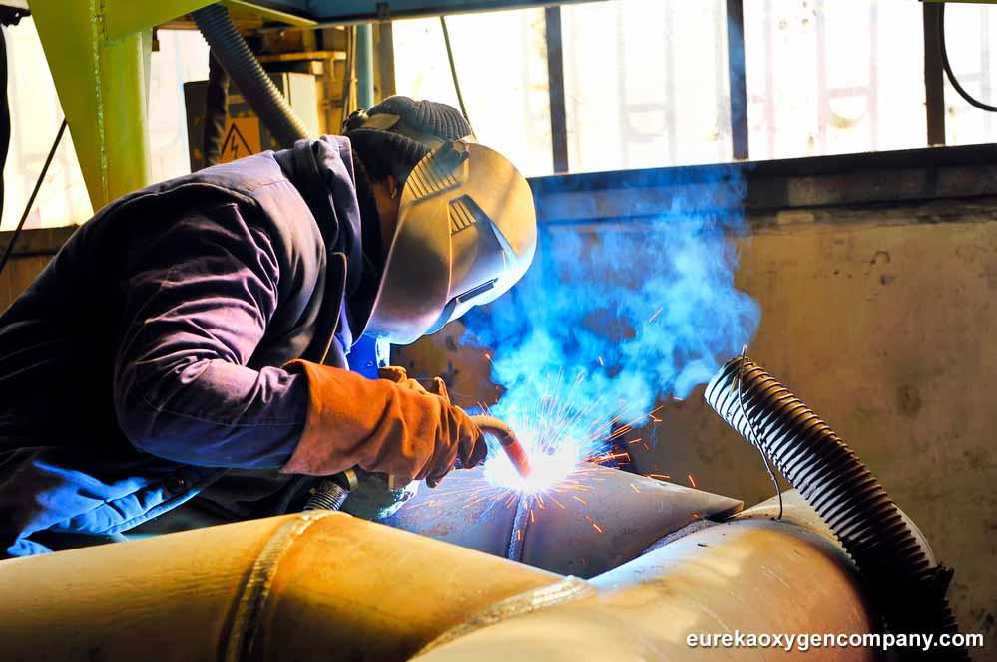
Shielding gas
There are two major solutions in the context of the best shielding gas for MIG welding mild steel. The first is a mixture of 75% argon and 25% CO2 that creates minimal spatter, offers the best bead appearance, and doesn’t promote the burn-through of thinner metals like mild steel. Alternatively, some welders use 100% CO2 which produces a deeper penetration, but invariably creates a lot of spatter.
Let us now examine the various technological advances gained in welding mild steel, particularly in the commercial and manufacturing industries.
Resistance spot welding technology
Resistance spot welding technology isn’t an altogether novel innovation. It was first invented in the early 1900s. Nevertheless, it has risen from its humble beginnings to become one of the most sophisticated automated welding processes currently to be had in the market. Resistance spot welding is known for the many advantages it offers when compared to most other welding processes including its low cost, speed, and strength in terms of joining sheet metal like mild steel.
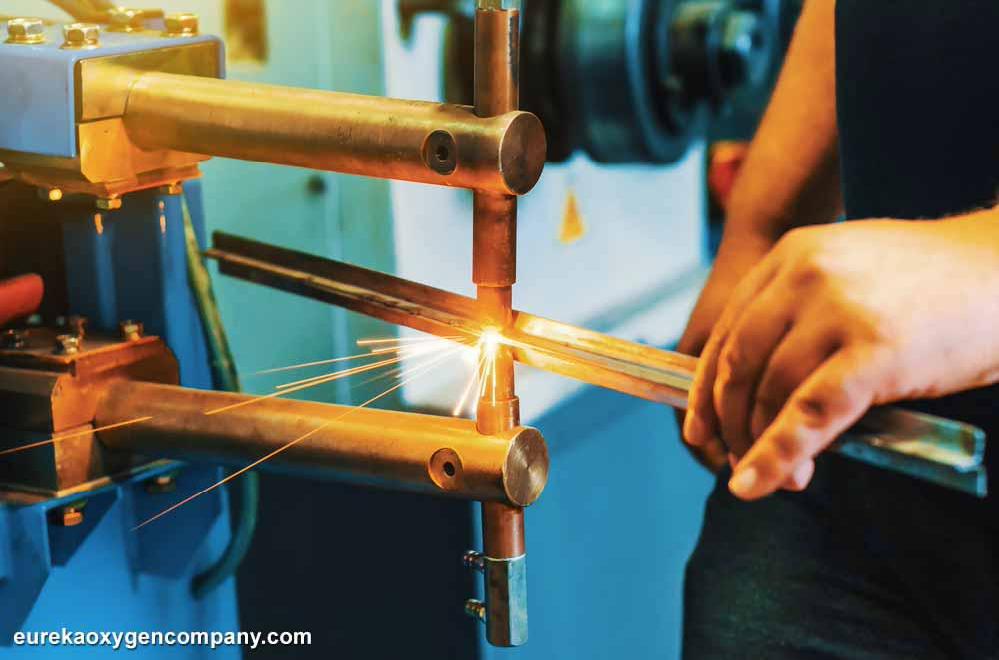
It is also very effective in eliminating distortion and warping of welds and its joints are extremely uniform. Resistance spot welding can support either semi-automatic or automatic welding and doesn’t require a highly-skilled welder to carry it out properly. With the passage of time, a number of technologies have spurned off this welding method. At the moment the most hyped is the use of ultrasound inspection when it comes to testing spot welds in metal sheets such as mild steel.
Laser welding technology
Laser welding technology has revolutionized many industries in the last 30 years. It is renowned for its unparalleled speed, flexibility, compatibility with diverse materials and thicknesses, low distortion, and low heat input. Laser welding also produces deep narrow welds. This makes it a feasible solution to produce joint configurations that most other welding methods are hard-pressed to create. One of the most innovative technological advances in laser welding has been made in the automotive industry. The patented BrightLine Weld technology allows a highly flexible range of parameters in the context of optimizing energy efficiency in welding vehicle components.
Eureka Oxygen is a foremost vendor of welding equipment, welding supplies, welding PPE, and accessories. We also offer a variety of quality industrial equipment and industrial gases.