Welding happens to be an intricate technical process. Even the most experienced of welders are known to make mistakes from time to time despite their skills and expertise. Being able to avoid common welding mistakes is always critical. This goes a long way in ensuring that you churn out consistently top-quality welds all the time. It also makes sure you can prevent welding-associated accidents and injuries. Generally speaking, accidents usually occur when precautions aren’t taken like when a welder fails to wear personal protective equipment. Besides this, mistakes may result in mounting operational costs that necessitate using more filler metals, raw materials, shielding, and even energy. Here are some of the most common welding errors and how you can effectively avoid them.
Poor preparation
Inadequate preparation in welding processes is noted for giving rise to a number of weld quality challenges. Oftentimes, welders (even the seasoned ones) commence this process before taking the necessary time to ensure they make the right preparations first, including properly preparing the metals they work on. This normally ends with rust, paint, dirt, and other contaminants being left present in the weld area and weld metal.
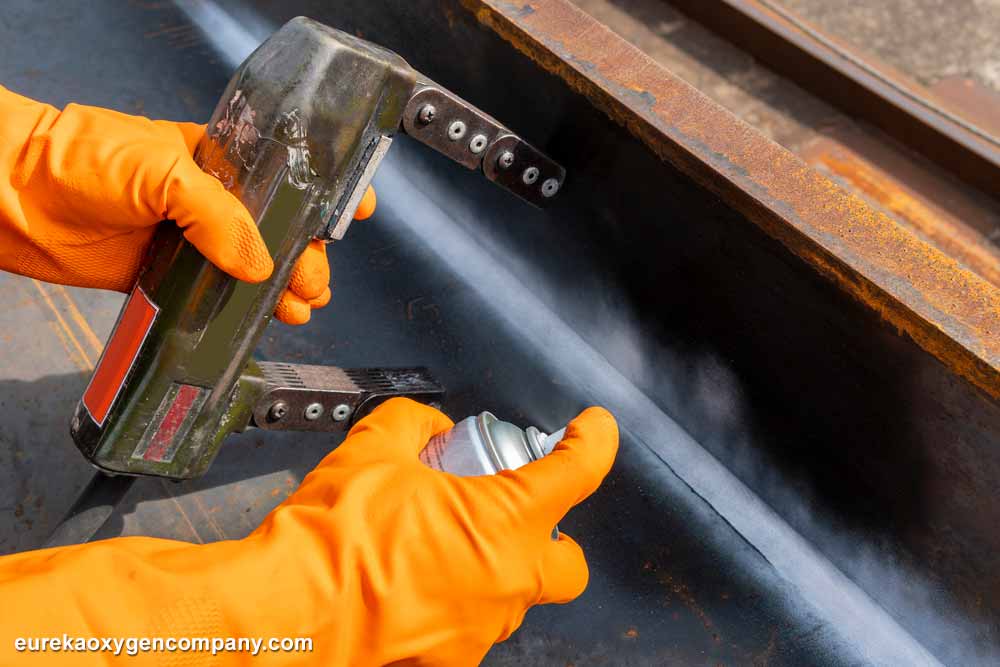
Also, proper welding preparation includes grinding out any cracking present on the metal, which might be invisible to the naked eye. To be able to obtain robust and contaminant-free welds, welders must take all the time they require to clean and grind the materials they weld appropriately. At the same time, it is important to note that some metals have to be cleaned more comprehensively than others such as aluminum to achieve satisfactory welding results.
Failing to take the right welding safety precautions
Essentially, safety is always paramount once undertaking the welding process. When a welder fails to take the required precautions, accidents along with injuries do invariably happen. While you might be able to rectify the effects of weld mistakes, some of the welding-related injuries may prove to be permanent or irreversible. This includes permanent vision impairment, dismemberment, hearing loss, the arc burns to mention just but a few.
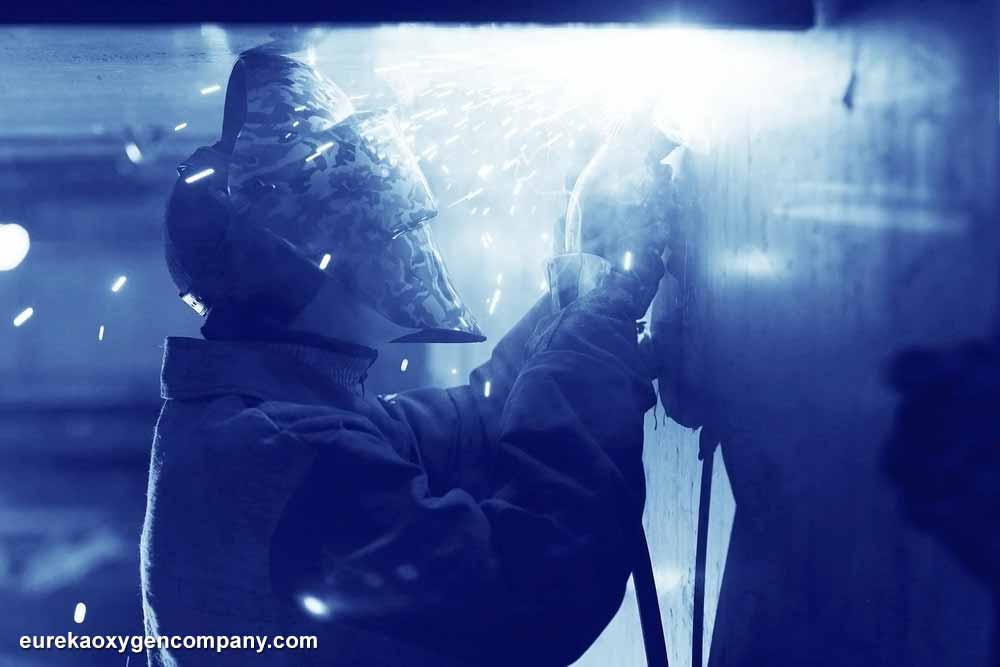
To be in a position to avoid these problems, welders must always use the recommended welding personal protective gear. This includes welding helmets, goggles, fire-proof garments and aprons, respirators, safety boots, gloves, and so on.
Improper handling and storage of filler metal and other welding consumables
One very common error welders routinely commit, including more experienced welders, is storing filler metals in areas where they are prone to contamination. This includes exposure to oil, grease, dirt, and even moisture. All this contamination, if left unchecked will in the long run negatively affect the overall welding performance. To be able to churn out quality welds, which aren’t susceptible to sustain damage, always store your filler materials and other consumables in clean and dry areas that are temperature controlled. Additionally, ensure you wrap wire spools and coils with airtight protective bags.
Using the wrong electrodes and wires
Despite the welding technique you make use of, it is always essential to use the ideal electrodes and wire for it. Different welding applications necessitate electrodes made specifically for them. Therefore, using the wrong ones which aren’t designed for the application you have in mind will usually result in many quality weld issues.
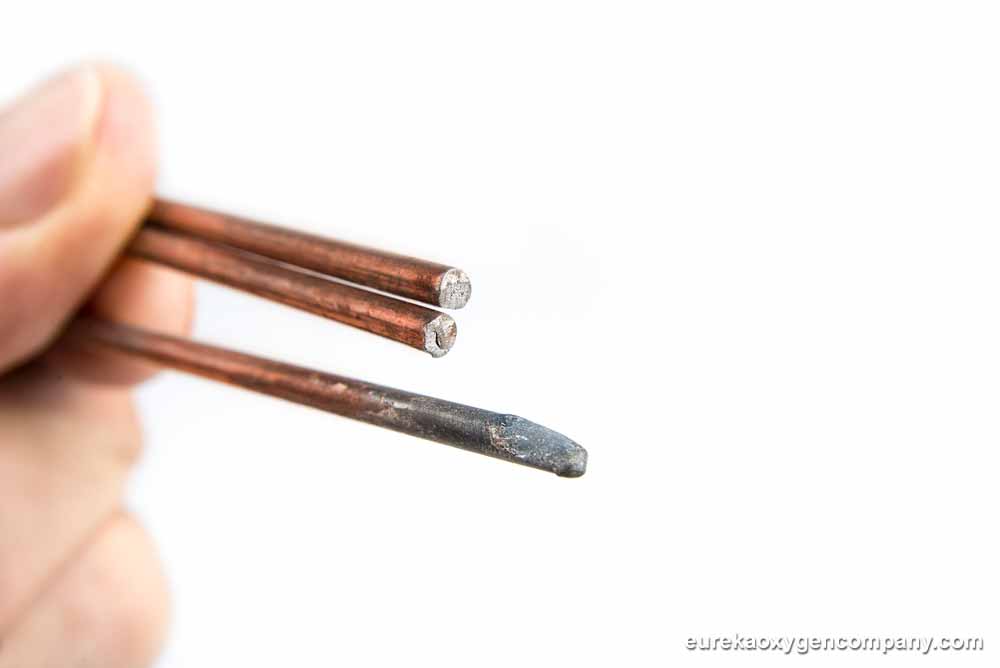
Using the wrong welding gun size
When you fail to utilize the suitable welding gun (one that is either too low or too high in amperage), there is always the risk of incurring extra operational costs and having to replace welding supplies and equipment. It is highly advisable to settle for a welding gun which is slightly lower than average in amperage in certain applications. For instance, you may minimize fatigue downtime and ensure maximum maneuverability by using a 200 amp gun rather than a 300 amp gun. Besides prolonging the lifespan of welding guns, using lower amperage will enable you to significantly cut down on operational costs too. Yet, it will be impractical to make use of a low amperage gun for an application that demands higher than average amperage. Doing so will trigger issues like premature weld failures.
Using the wrong voltage and wire feed speed
Using the wrong voltage or wire feed speed leads to very erratic arcs. Also, when excessive heat is generated in a welding gun’s handle, it will ultimately trigger challenges with the contact tip. Setting the speed of wire feed too fast will cause the wire to build up rather than melt as required into the weld pool. This can trigger birdnesting or even burnback. Alternatively, setting the wire feed speed too slow often results in missing the penetration necessary for quality welds. To circumvent these problems, it is always prudent to strictly follow the instructions of your welding gun’s maker when it comes to the right voltage and wire feed speed for the welding applications and materials you want to utilize.
Eureka Oxygen is a foremost vendor of top-notch welding equipment, welding supplies, and a variety of industrial equipment and industrial gases. We offer options for all types of welding and our in-house experts are here to meet your needs for any job!