1. Falls
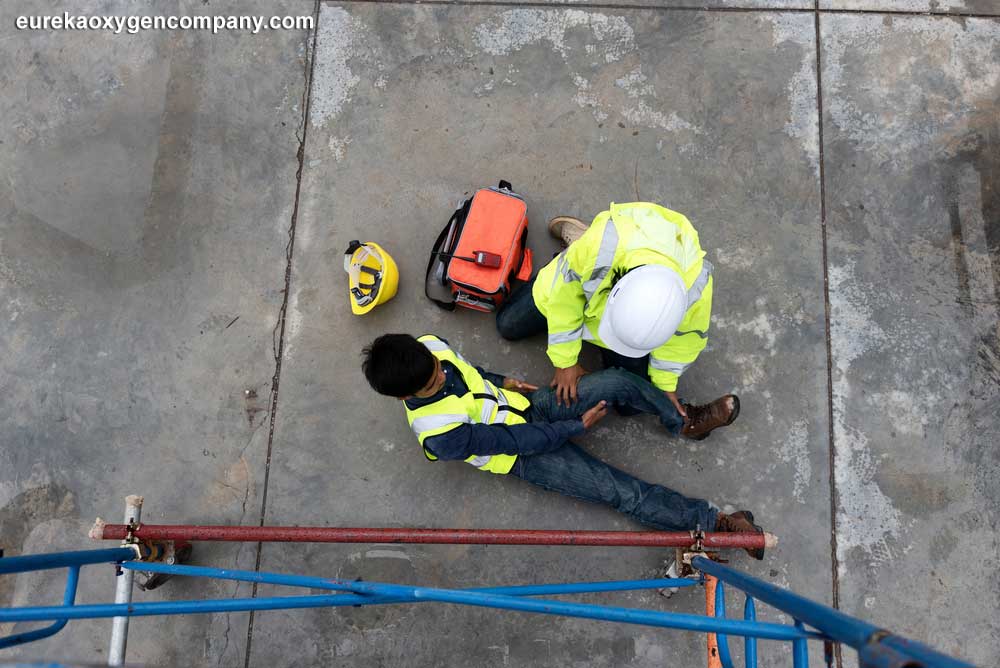
The leading factor in construction work fatalities is falling. According to OSHA statistics, falls represent over one-third of all private sector employee fatalities. To this end, OSHA enjoins building firms to fully comply with its Fall Protection Standard. Employers are held responsible to put in place policies that safeguard employees from falls related to overhead platforms, uplifted workstations, and floor holes. Among other things, this entails meticulous planning of jobs and the provision of fall protection equipment for employees who work 6 feet or more above lower levels. As for the prevention of falls, companies are admonished to carry out regular inspections of ladders, scaffolding, and safety equipment including personal fall arrest systems (PFAs).
2. Hazardous materials
The leading factor in construction work fatalities is falling. According to OSHA statistics, falls represent over one-third of all private sector employee fatalities. To this end, OSHA enjoins building firms to fully comply with its Fall Protection Standard. Employers are held responsible to put in place policies that safeguard employees from falls related to overhead platforms, uplifted workstations, and floor holes. Among other things, this entails meticulous planning of jobs and the provision of fall protection equipment for employees who work 6 feet or more above lower levels. As for the prevention of falls, companies are admonished to carry out regular inspections of ladders, scaffolding, and safety equipment including personal fall arrest systems (PFAs).
3. Scaffolding
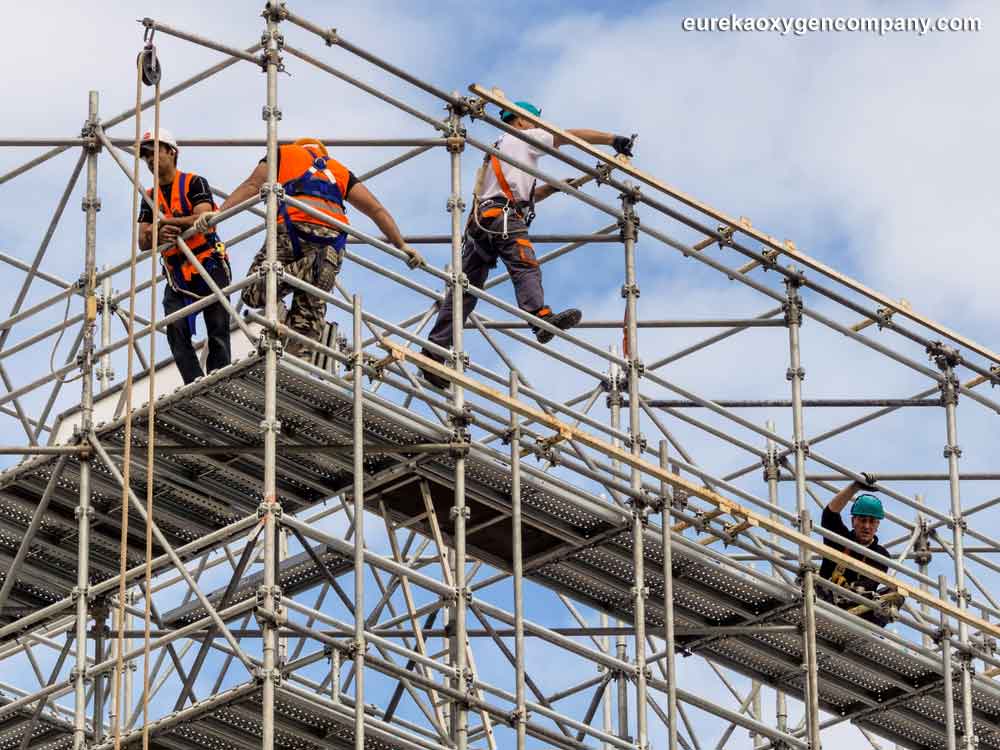
Scaffolding safety is very integral in the prevention of falls. The OSHA Scaffold Standard dictates scaffolds as well as their components, besides their own weight, must effectively support no less than four times the maximum load without falling. Companies are required to conduct inspections of scaffolding construction on a daily basis and ensure they adhere to OSHA standards.
4. Lockout/tagout
5. Respiratory hazards
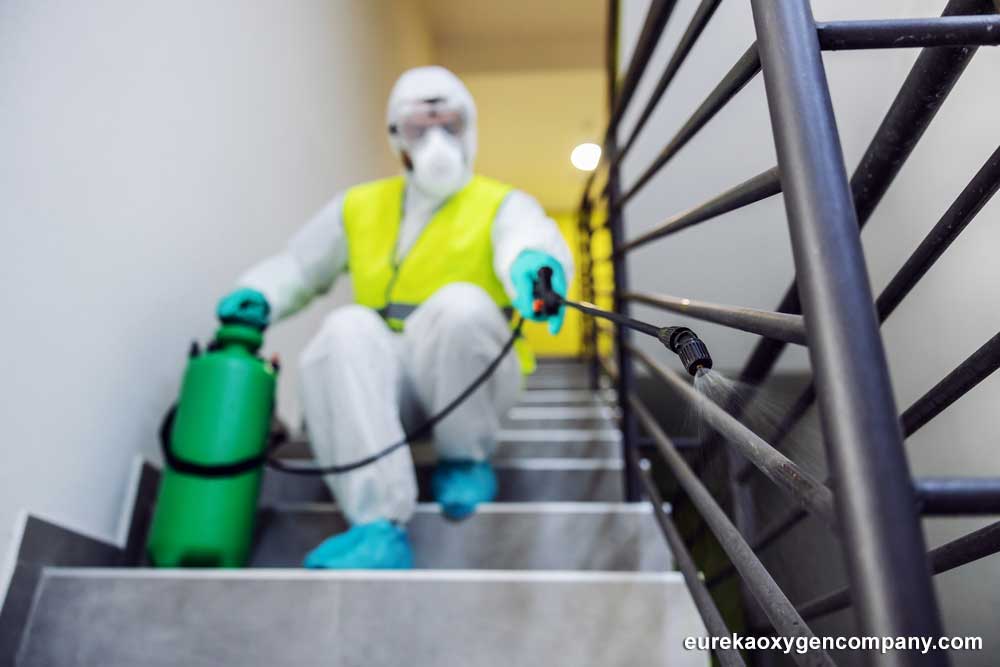
6. Ladder hazards
7. Powered industrial truck hazards
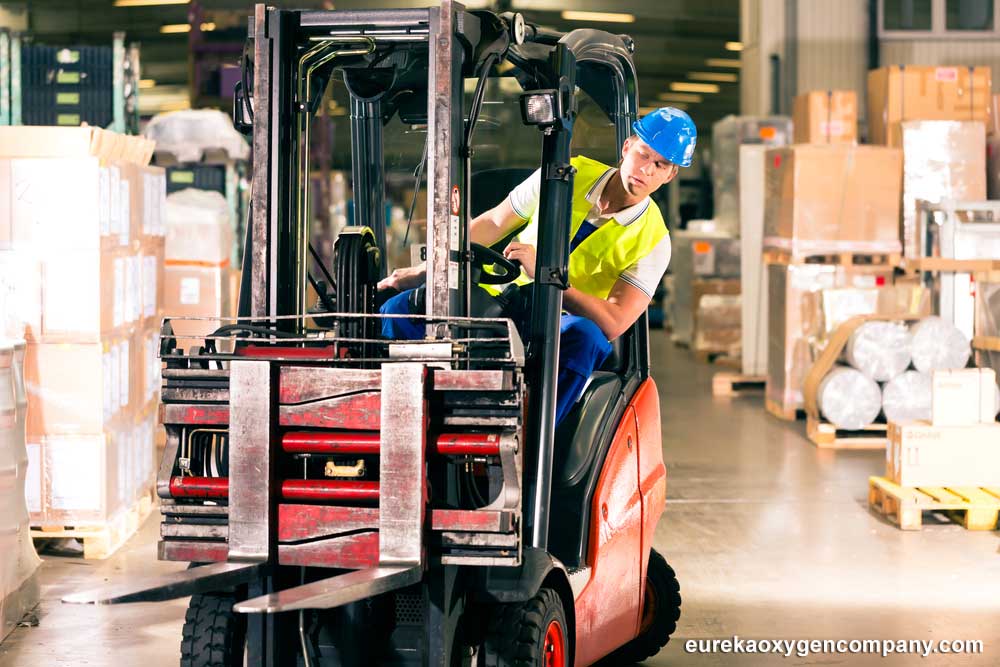
8. Fall protection
Since falls represent the most common cause of worksite-related injuries, OSHA severely penalized employers who fail to comply with OSHA Training Requirements for Fall Protection. Companies are obliged to provide proper training to workers who are vulnerable to fall hazards. They are also required to validate compliance with a written certificate containing trained workers’ names, training dates, and employer signature.
9. Machine guarding
When barrier guards, electronic safety devices, and two-handed tripping devices aren’t correctly used, employees are at an increased risk of sustaining serious injuries. Companies are required to provide employee training on OSHA Machinery and Machine Guarding Standard and guarantee guard utilization doesn’t trigger its own safety hazards.
10. Eye and face protection
According to recent statistics from the CDC, every day nearly 2,000 employees in the US sustain work-associated eye injuries which necessitate medical care. Companies are mandated to provide proper PPE that plays a critical factor in the prevention of eye and face injuries. Also, welding curtains can prevent arc flashing, while goggles and face shields deliver much better protection from impacts. Should a worker wear prescription eyewear, employers must guarantee they always don eye protection that accommodates their glasses or integrate the prescription lenses into its design. Eye protection processes must include eyewash stations and training on OSHA’s Eye and Face Protection Standard.
Eureka Oxygen is a noted vendor of top-notch welding equipment and welding supplies including welding pliers along with many other welding-related accessories.