The use of argon in welding traces back to the 1920s when automatic welding was first introduced. Argon-oxygen blends are widely used for conventional and pulsed spray transfer on clean, plain carbon and stainless steel, and both kinds can benefit from the use of argon-oxygen gas blends. These blends are typically 1, 2 or 5% oxygen and provide good arc stability and very low levels of spatter and fume.
Principal Applications
Argon-oxygen blends are generally used for welding heavy section carbon steel for farm equipment, ships, and automotive assemblies. These blends are also used for spray arc welding of both ferritic and austenitic stainless steel components. Argon-oxygen blends with 1–2% oxygen are used when you need low carbon content in the weld.
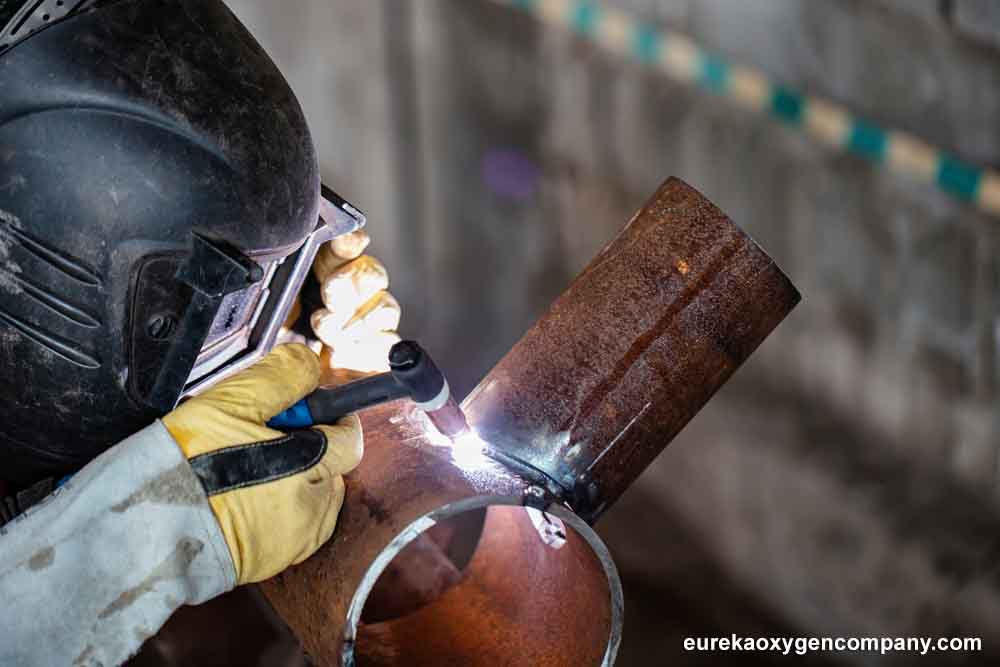
Argon-Oxygen Blends
Argon-Oxygen 99% to 1%
A blend with 1% oxygen is primarily used for spray transfer on stainless steel as that amount is generally sufficient to stabilize the arc and improve the droplet rate and bead appearance.
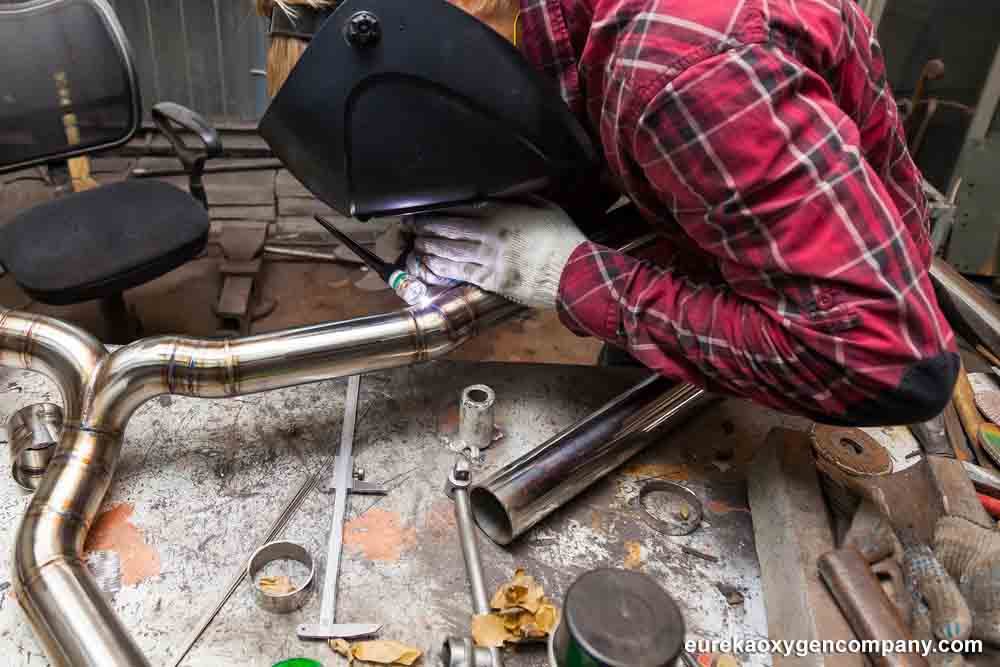
Argon-Oxygen 98% to 2%
A 2% oxygen blend is an ideal choice for spray transferring stainless steel. It is used for spray arc welding of carbon and low-alloy steels. It creates a greater wetting action than the 1% oxygen mixture, however, bead appearance will be darker and more oxidized for the 2% blends with stainless steels.
Argon-Oxygen 95% to 5%
A 5% oxygen blend is the most commonly used argon-oxygen mixture for general carbon steel welding. This welding blend provides a more fluid but controllable weld pool, and you will see higher travel speeds. Anything higher than 5% oxygen will oxidize an electrode without deoxidizers.