Making a great weld is about more than making it “pretty” – although, the processes that go into making it pretty are more important to its quality than aesthetic considerations. Depth, width, crown – all need to be consistent throughout and adequate and appropriate to the materials being joined. It can be done, and here are some tips to ensure you do it.
Clean the material to be welded before starting. Don’t think, “It’s going to get slag on it anyway” because if you choose your shielding gas properly, it won’t. So, wipe or scrape away any dust, oil, grease, paint, rust, or other contaminants before the first feed, the first arc. A clean cloth, sandpaper, or a wire brush should be all you need. Do not use cleaning solvents, unless your fire insurance and life insurance is paid up. They’re flammable and your arc is an ignition point.
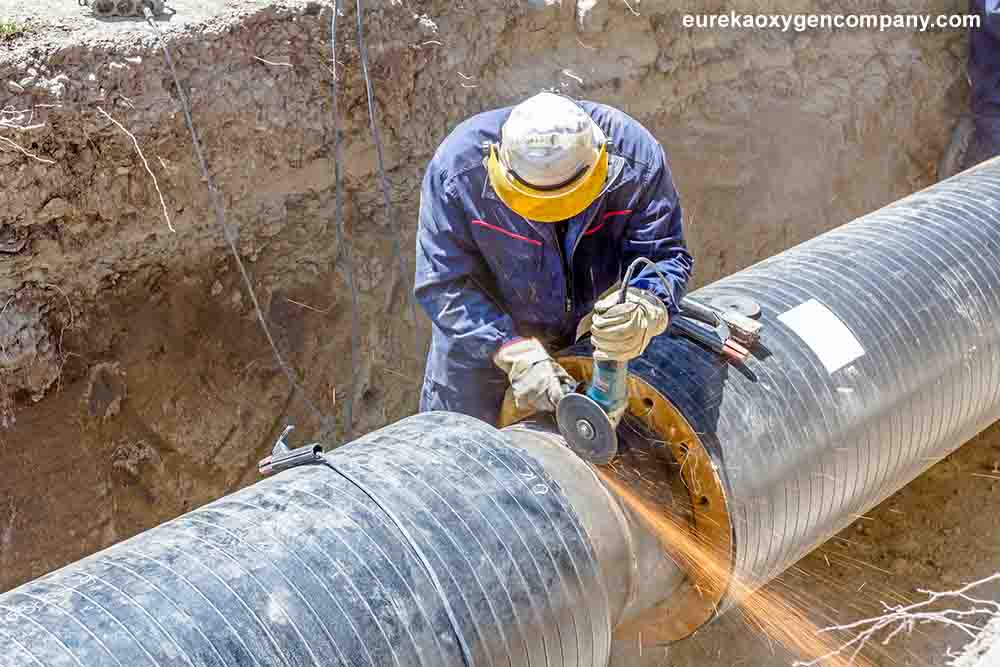
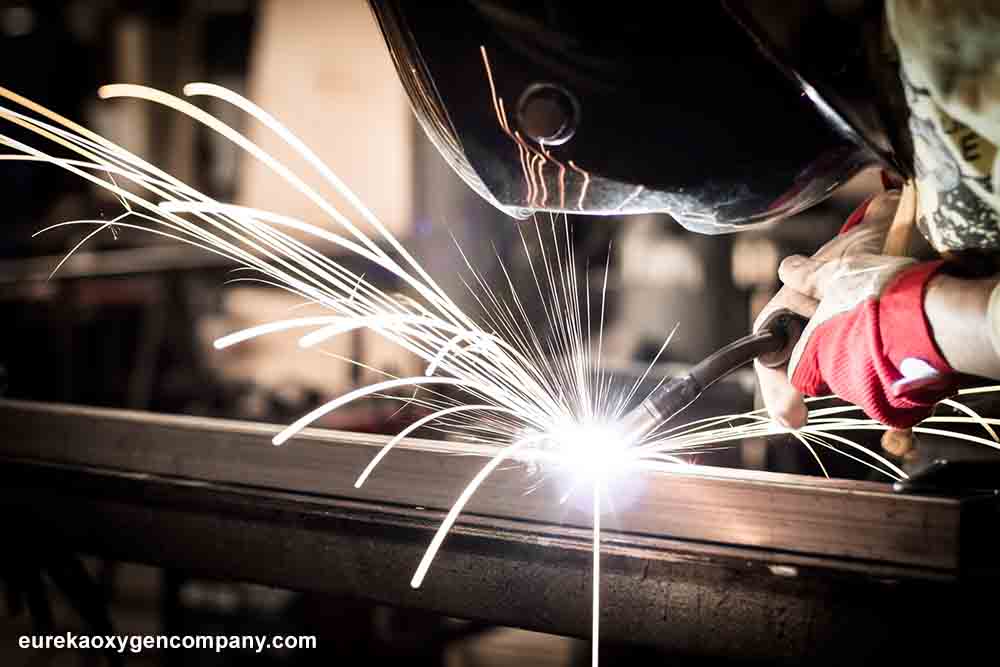
As already mentioned, under cleaning, choose your shielding gas per the manufacturer’s recommendations for the filler wire you are using. In this way, you will achieve slag-free welding. Set the power source to the specified settings per the wire manufacturer’s recommendations for wire polarity. Weld quality may suffer if you fail to do so.
Follow the wire manufacturer’s recommendations for wire feed speed and voltage. Failure to do so will almost certainly adversely affect the resulting weld. Too fast could cause excess metal deposits (wasting costly filler metal) or result in burn-through. Too slow may result in a weld that does not penetrate or fill the joint properly. A setting too fast or slow could cause the wire to “burn-back,” or melt at the tip. With the voltage setting, there are also adverse effects from too high or too low. Too high a voltage setting will contribute to spatter and a weld that is too wide, too flat, and too porous. It can also cause undercutting — a groove melted into the material that is not properly filled. Too low a voltage setting, on the other hand, just produces a narrow weld bead that lacks proper penetration and fusion. Both extremes contribute to a weld that is not only unaesthetic but structurally unsound as well.
Make sure your stick-out is the appropriate length – the stick-out of the electrode being the amount of un-melted wire protruding beyond the tip of the gun. This distance is determined by the diameter of the wire being used. General guidelines to use as a starter are: 0.024- and 0.030-inch wire requires 1/4- to 3/8-inch stick-out; 0.035- and 0.045-inch wire requires 3/8- to 1/2-inch stick-out. But don’t just “set it and forget it.” Listen to the sound of the weld/welder. Too much popping or cracking means too much stick-out. Adjust accordingly.
Last, but in no way least, pay careful, constant attention to the position of the wire over the weld as you make it. This involves the work angle and the travel angle. The work angle is the angle at which the wire is pointed at the weld. For lap and t-welds, that angle should be 45 degrees, while for butt welds it should be 90 degrees.
The travel angle, as the name implies, is the angle of the wire as it travels along the weld path. The norm for travel angle is a drag angle of 13-30 degrees – meaning that the back of the gun in your hand is ahead of the wire tip at an angle of that many degrees as you travel along the weld (like the wire tip were being dragged, as opposed to being pushed or floated).
Making attractive welds may not be at the top of your list, but improving your technique will allow for consistency and stronger welds. Eureka Oxygen offers a variety of welding gases to help you practice and improve your welds and therefore your projects.