It’s all about integrity – not the welder’s, the weld’s. If you want a weld that is structurally sound – both now and in the long run – you want to implement a welding process that is gas-shielded. The weld pool or puddle is, during its creation, a very malleable and permeable thing – susceptible to the intrusion of contaminants in the form of ambient gases in the atmosphere.
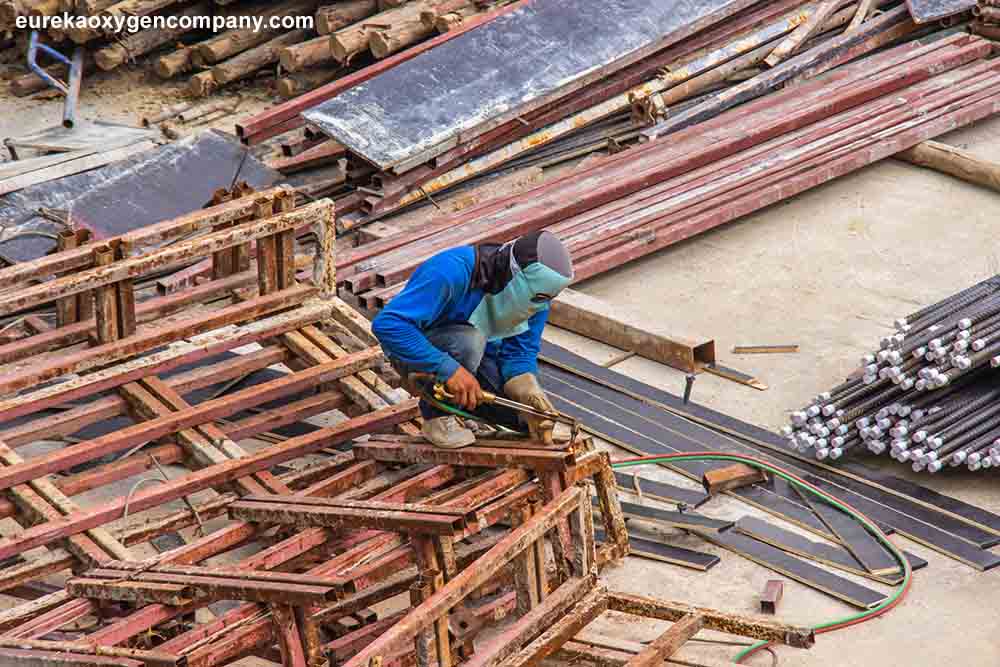
The saying goes, “rust never sleeps.” Rust is just oxidation – the addition of oxygen to the metal to which it attaches. Oxygen never sleeps, and either do nitrogen or hydrogen. Together, these three gases represent the majority of our atmosphere here on Earth. They also represent the three most likely (and insidious) culprits in the contamination of welds. Microscopic-level porosities in the weld material may not be readily evident to the naked eye, but they become manifestly evident when the weld in which they have occurred fails.
To avoid this eventuality, the welding industry developed the use of shielding gases – gases that displace the oxygen, hydrogen and nitrogen from the vicinity of the weld while it is being formed. Argon, Helium, Carbon Dioxide and Oxygen are the most common gases used for shielding in MIG welding. The selection of a specific shielding gas – or blend of gases – is crucial to and dependent on the specific welding application for which it is chosen.
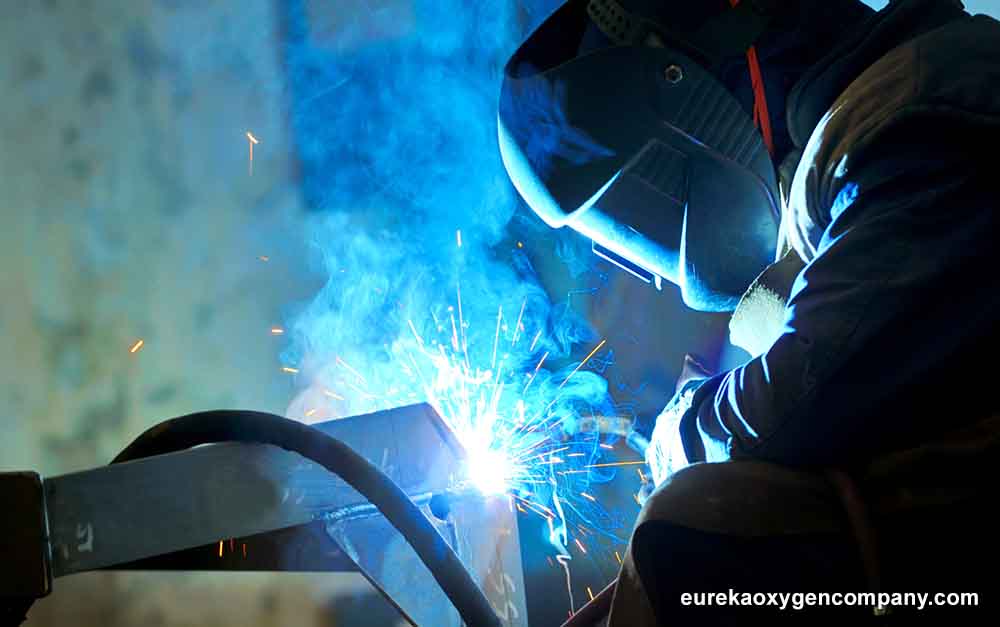
Carbon dioxide is the most commonly used (and cheapest) of the shielding gases. Its applicability is limited to the short circuit process, however, and when used by itself it generates more spatter and a less stable arc. However, it does work well with thick material due to its very deep weld penetration.
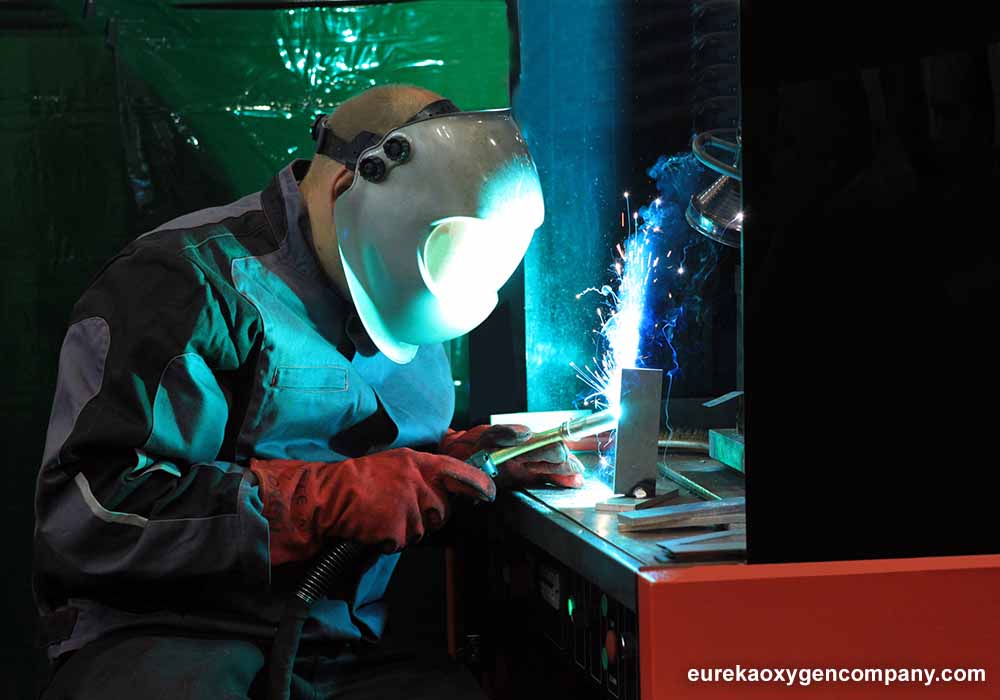
Carbon dioxide’s range of use is expanded considerably by the addition of Argon to the mix. This results in improved weld quality and reduced clean-up. The mix ratio can range anywhere from 95/5 to 75/25 (Argon/CO2), depending on the specific application. This mixture enables the use of a spray transfer process, which improves productivity and appearance (of the finished welds). It also produces a narrower penetration profile – useful for fillet and butt welds. But if you’re welding a non-ferrous metal, you will need to switch to pure Argon.
Helium, like Argon, is typically used with non-ferrous metals. However, it can also be used with stainless steel. Its mix ratio with Argon can range from 75/25 to 25/75 (Helium/Argon). That ratio will determine the penetration, bead profile, and travel speed for your welds. In general, travel speed with helium is faster, as it provides a hotter arc. That faster speed does translate into higher productivity rates, but those rates come with a cost – both in the base cost of Helium and in the higher flow rate that its use requires. If you choose to use Helium with stainless steel, it is normally implemented in a tri-gas mix with Argon and CO2.
If this all seems like TMI about MIG, or if you are still uncertain as to which gas, pure or mixed, is best for your specific application, feel free to contact the pros at Eureka Oxygen for further advice. Whatever you decide you need for your welding application, we can provide it for you.