First off, let’s make a quick distinction between MIG (Metal Inert Gas) and TIG (Tungsten Inert Gas) welding. The difference may seem obvious in their titles. One uses metal and the other, tungsten. However, the form of those materials in the two processes is radically different. The metal used in MIG welding is a continuous-feed wire, which becomes filler for the weld. The tungsten used in TIG is a non-consumable electrode which heats the two surfaces to be welded sufficiently to join them without filler.
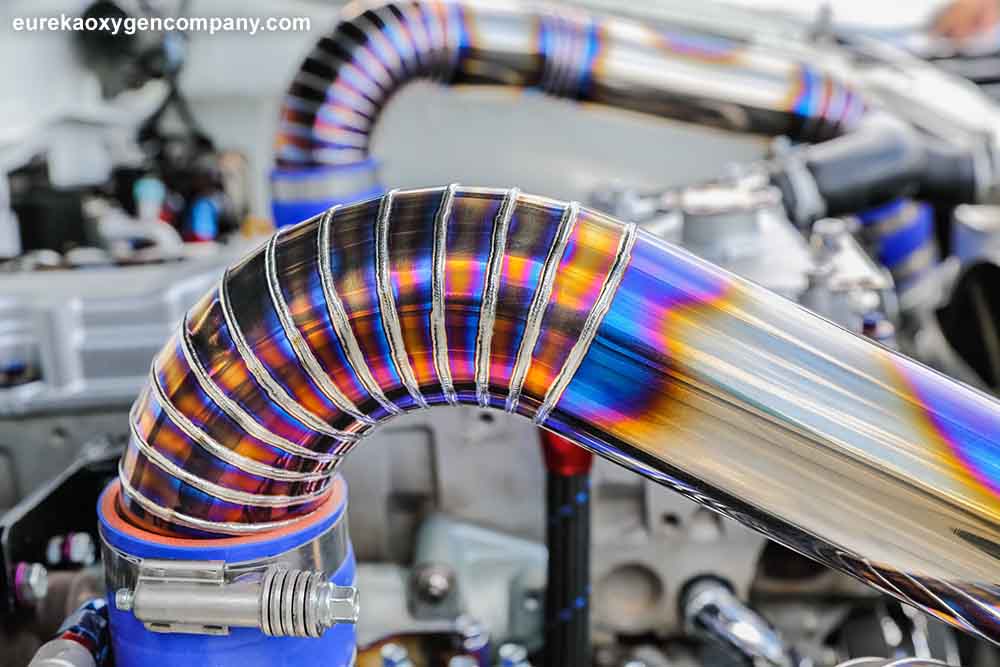
So, when and why would you choose TIG welding? It can provide a cleaner, neater weld, but because of the higher heat required, it can also blow out the weld in a variety of ways. Greater skill – and optimally, the use of CNC (computer numerical control) – is required. Still, there are specific job requirements which mandate or at least recommend the use of TIG.
Let’s start with the list of when not to use TIG, based on the job requirements:
- Are the metal pieces to be joined thick? If yes, use MIG. Heating thicker metal pieces all the way through to a stage that creates a satisfactory weld, without the use of filler, is problematic.
- Are the metal pieces ductile (capable of electrical conduction)? If yes, use MIG. Arc welding depends on electrical resistance to create the heat that creates the weld. Without filler material, it takes a lot more electrical energy to generate a satisfactory weld.
- Are the metal pieces of two different types of metal? If yes, use MIG. While welding of dissimilar metals is generally discouraged, when it is necessary, a satisfactory weld will be dependent on the filler material that joins the two pieces.
The fourth criterion in this checklist is the one that most clearly indicates the advisability of TIG:
- Is surface condition and smoothness a primary concern for the finished product? If yes, consider TIG. The filler material provided by MIG can more easily create a solid bond between the two metal pieces being welded, but it can also disperse spatter on their surfaces. Cleaning up those defects after the fact can be time-consuming and less than perfect. If a pristine finished product is required, TIG may also be required.
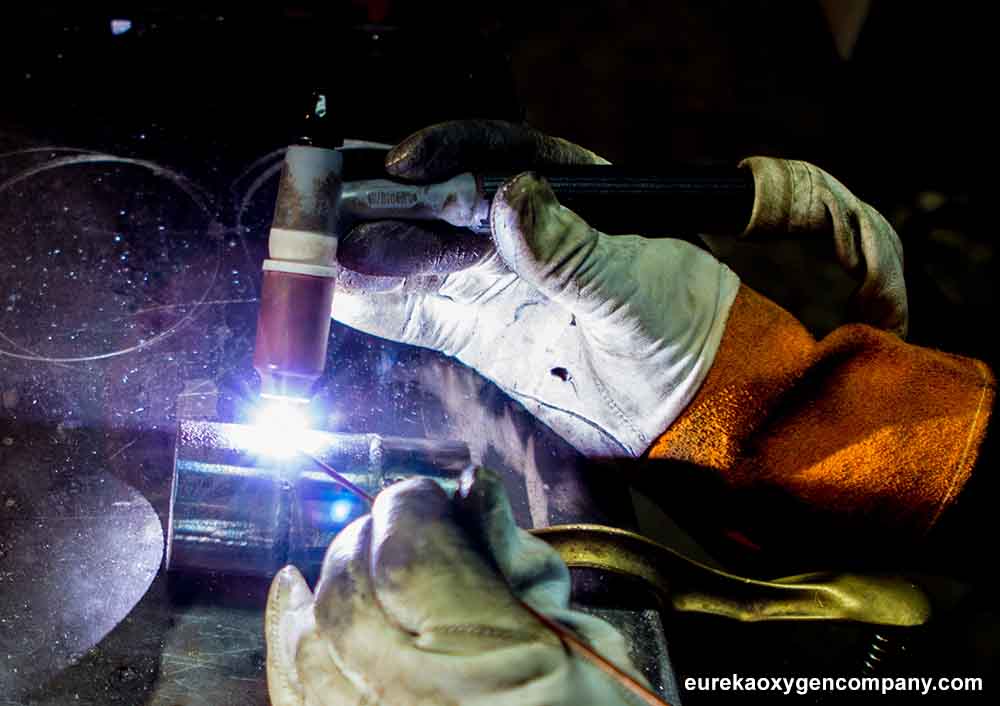
So, if your project involves thinner metal that is relatively non-conductive and the goal is a spatter-free, smoothly-welded finished product, consider TIG. Your friendly welding pros at Eureka Oxygen can provide you with all the specifics and equipment you need to do the job right.